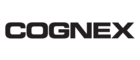
Chez MPC, les Checker de Cognex évitent les défauts d’assemblage et améliorent la productivité
19/11/2008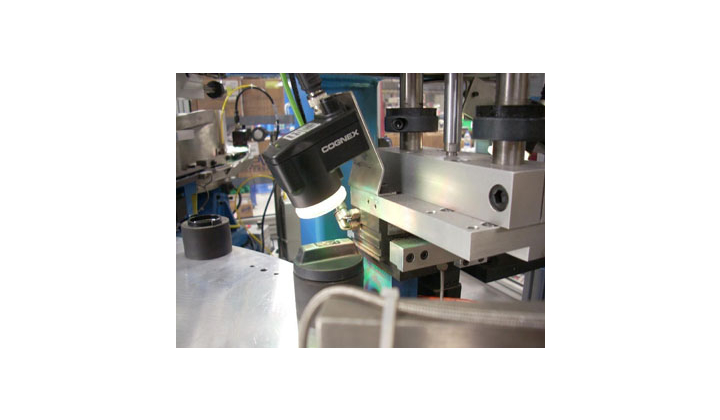
Pour contrôler les éventuelles erreurs sur la ligne d’assemblage automatisé de bouchons d’huile de son site de Prairie du Chien, Miniature Precision Components Inc. utilise trois capteurs de vision Checker de Cognex.
MPC fournit l’industrie automobile en pièces et assemblages moulés par injection de très haute qualité. Le fabricant s’est vu décerner plusieurs fois le prix Ford Q1 Preferred Supplier et a reçu de nombreux trophées de la part de GM, Nissan, Harley Davidson et Chrysler. Le site de Prairie du Chien est équipé de 41 machines de moulage de 25 à 550 tonnes.
" L’automatisation nous a permis d’atteindre un haut niveau de qualité ; et la vision industrielle a été un élément-clé de notre stratégie d’automatisation au cours des sept dernières années," explique Shane Harsha, MPC Manufacturing Engineering Manager. La preuve par l’exemple avec le système d’assemblage automatisé de bouchons d’huile, où les traditionnels capteurs équipant les machines ont été complétés avec des capteurs de vision Checker de Cognex. Avec comme résultat une amélioration très sensible de la répétabilité, et donc une production plus efficace de bouchons d’huile sans défaut. "Les capteurs de vision Checker sont très simples à installer et à configurer ; ils constituent une option très économique pour effectuer des inspections lorsque les capteurs traditionnels ne sont pas fiables et qu’un système de vision complet coûterait trop cher," ajoute Shane Harsha.
La chaîne d’assemblage de bouchons d’huile de MPC installe des joints toriques sur des bouchons thermoplastiques moulés, puis imprime une marque sur la face supérieure de ces bouchons.
Le contrôle minutieux de l’orientation du joint torique et du bouchon est essentiel pour garantir le bon positionnement du joint et donc l’étanchéité du bouchon d’huile. Pour garantir une qualité rigoureuse, le bouchon doit également être orienté correctement avant le marquage. Les contrôles mécaniques et les capteurs traditionnels s’étant avérés peu fiables, MPC a choisi, après test, trois capteurs de vision Checker pour garantir la bonne orientation des joints toriques et des bouchons.
Un premier capteur Checker vérifie que chaque joint torique est orienté correctement au moment où il est chargé sur le plateau d’assemblage. Un joint torique mal orienté doit être écarté de la ligne d’assemblage et remis dans le circuit. En effet, si un joint est positionné à l’envers, la machine s’arrête et l’opérateur doit alors accéder au joint et le repositionner avant de redémarrer la machine.
Un deuxième capteur de vision Checker vérifie que le joint est bien positionné avant que le bouchon ne soit appliqué. Un troisième contrôle la bonne orientation du bouchon avant assemblage et marquage ; si ce n’est pas le cas, le capteur de vision envoie un signal qui fera pivote le bouchon de 180 degrés avant son positionnement sur le plateau d’assemblage.
"Les capteurs de vision Checker nous ont aidés à atteindre des taux de zéro défaut dans le processus de fabrication et à réduire les rebuts," conclut Shane Harsha. «Ils représentent la solution parfaite pour la plupart de nos applications d’inspection et de contrôle des erreurs."