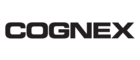
Borg Warner choisit une solution de traçabilité estampillée 100% Cognex
04/02/2008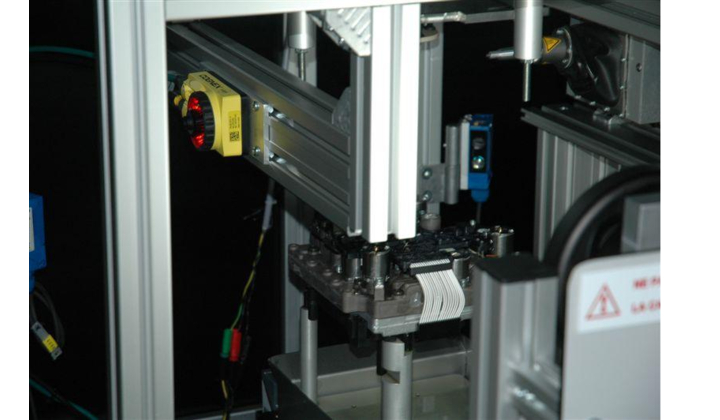
Fournisseur des plus grands constructeurs et équipementiers automobiles, Borg Warner a choisi Cognex pour assurer la traçabilité d'un d’un nouveau composant à très forte valeur ajoutée.
Fournisseur des plus grands constructeurs et équipementiers automobiles, Borg Warner n’a pas droit à l’erreur. Pour garantir la qualité d’un nouveau composant à très forte valeur ajoutée et pouvoir le suivre tout au long de son cycle de vie, Borg Warner choisit de le tracer de bout en bout.
La société se tourne vers Cognex dont les systèmes de vision équipent déjà bon nombre de ses lignes et de ses machines de production. Pas moins de trois partenaires de Cognex collaborent à ce projet piloté par Alema Automation, PSI (Partner System Integrator) de Cognex pour le Sud-Ouest de la France.
Il s’agit de marquer chaque pièce, vérifier l’exactitude et la qualité du marquage puis s’assurer, avant expédition, qu’elle a franchi avec succès tous les contrôles requis. La solution : un système de vision VisionPro et des capteurs In-Sight 5110 de Cognex, un logiciel « Cognex Partner Product » (CPP) développé par Esox, autre PSI de Cognex et des machines de micropercussion de Technifor, lui aussi partenaire de Cognex…
Gravé à vie dans le métal
A la sortie de la ligne de production, chaque pièce « brute de fonderie » est marquée par micropercussion : deux lignes de caractères alphanumériques indiquent la référence du produit, le numéro du lot dont il fait partie, l’équipe, la date de fabrication…
Un premier poste de vision constitué d’une carte 8500 et de VisionPro (la bibliothèque d’outils de vision de Cognex) lit ces caractères grâce au logiciel d’Esox. Et les transmet à une graveuse Technifor qui les convertit en DataMatrix et grave ce code sur une autre face de la pièce.
« Le logiciel d’Esox est utilisé avec succès dans l’industrie automobile. Il nous a permis de respecter budget et délais », explique Olivier Skalinski, responsable du projet chez Alema.
Pour éviter toute erreur et garantir sa tenue dans le temps, un premier capteur de vision In-Sight 5110, installé tout à côté de la machine de micropercussion, vérifie le contenu et la qualité du marquage.
Des tests suivis à la trace
Dûment gravée, la pièce est alors testée sur toutes les coutures, par rien moins que huit bancs de test hydrauliques… Au sortir de cette épreuve, elle est dirigée sur un deuxième poste de lecture In-Sight 5110. Il s’agit maintenant de vérifier qu’elle a bien subi tous les tests et que ceux-ci sont réussis. Et la tâche n’est pas simple.
En effet, si les pièces qui se présentent devant le premier poste de lecture In-Sight sont propres et sèches, elles sont, au sortir de l’épreuve bancs de test, ruisselantes d’huile... Pourtant, malgré des conditions de lisibilité et d’éclairage totalement différentes de la première lecture, l’In-Sight 5110 du second poste lit parfaitement le code inscrit sur chaque pièce, sans réglage complémentaire.
Alema Automation doit relever un autre challenge : faire dialoguer l’In-Sight 5110 avec la base de données de l’usine contenant le résultat des tests. La société développe pour cela une interface spécifique. Et l’In-Sight délivre son verdict pour chaque pièce : bonne, ou pas, pour l’expédition.
Les pièces en défaut mais réparables sont renvoyées pour rectification. Quant aux pièces ayant passé avec succès l’ensemble des tests, elles sont acheminées vers la zone d’emballage. Pour une sécurité maximale, Alema y a installé, à l’entrée, un troisième capteur de vision In-Sight 5110 qui effectue une dernière lecture/vérification.
Top chrono
L’application a été développée et installée par Alema Automation en un temps record : deux jours pour valider le fonctionnement de son système sur des pièces prototypes, puis une petite semaine pour son installation sur le site, la recette et la formation du personnel à l’utilisation et à la maintenance.
Une formule gagnante
La robustesse des capteurs In-Sight, leur capacité à s’affranchir des variations d’éclairage et d’aspect, ont permis d’utiliser le même matériel sur les différents postes de contrôle ; et par la même occasion de réduire sensiblement le stock de pièces de rechange de Borg Warner.
Autre bénéfice, et non des moindres, l’engagement d’Alema Automation sur la globalité du projet (lecture, marquage ET relecture) a évité les éventuels conflits entre fournisseurs distincts.
« Grâce à l’étendue de l’offre Cognex et à son réseau de partenaires, nous disposons d’une solution performante et au meilleur coût », conclut Stéphane Laval, du Service Assembly Process Engineering de Borg Warner.
Devant le succès de cette solution, Borg Warner envisage de modifier, selon le même principe, d’autres lignes de production afin d’en améliorer la traçabilité.