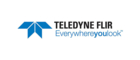
Une caméra acoustique assure la détection à temps des fuites d'air cachées
05/12/2023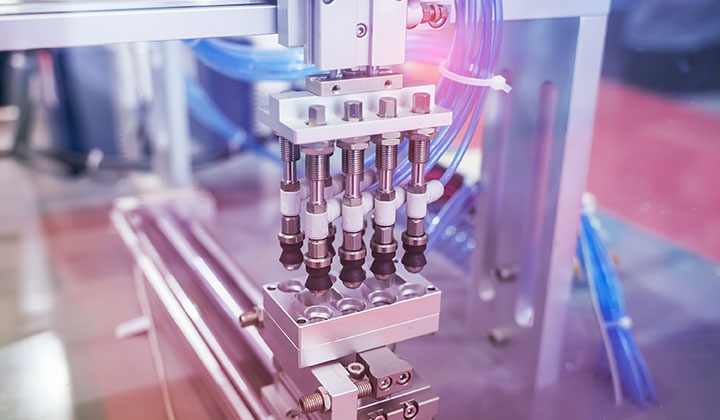
Une entreprise pharmaceutique internationale a découvert qu'une caméra acoustique est une méthode de maintenance prédictive fiable, rapide et facile à utiliser pour détecter les fuites d'air cachées dans l'usine et ainsi éviter des incidents graves et réduire les coûts
Les fuites d'air sont monnaie courante dans les environnements industriels. Selon des études sur les fuites dans les systèmes d'air comprimé, le taux de fuite moyen est d'environ 25%, mais certaines installations perdent jusqu'à 80% de leur air comprimé à cause des fuites. Si elles ne sont pas détectées et traitées à temps, ces fuites peuvent induire des coûts supplémentaires, des arrêts imprévus et même des risques potentiels pour la sécurité. Les endroits particulièrement exposés aux fuites d'air dans les usines et les installations de fabrication sont les canalisations, les tuyaux, les vannes et les interstices entre les équipements, où elles sont généralement invisibles à l'œil nu et ne peuvent être détectées qu'à l'aide d'un matériel spécialisé de surveillance d'état.
La solution idéale pour l’inspection rapide et fiable des fuites d'air
En utilisant une caméra acoustique dans le cadre de son programme de maintenance prédictive, l'entreprise pharmaceutique a pu prévenir les problèmes de sécurité potentiels et assurer la continuité opérationnelle en détectant les fuites d'air et de gaz dans l'usine. Outre les avantages évidents en termes d'économies de temps, de coûts et d'énergie, l'entreprise a été agréablement surprise par la facilité avec laquelle l'appareil a été intégré dans le cycle de maintenance, en ne nécessitant qu’une formation minimale.

Les avantages d'une caméra acoustique pour la détection des fuites d'air
• Economise du temps, de l'énergie et des coûts et réduit l'empreinte carbone en localisant à temps les fuites d'air comprimé cachées.
• Garantit la continuité opérationnelle grâce à la détection précoce des fuites d'air et de gaz.
• Scanne rapidement de vastes zones et localise avec précision les problèmes critiques, même dans des environnements industriels bruyants.
• Ne nécessite qu’une formation minimale et est facile à intégrer dans le cycle de maintenance.
• Fournit des résultats en temps réel et des données exploitables pour les plans de maintenance et de réparation grâce à des analyses basées sur l'apprentissage automatique.
Autres actualités Teledyne FLIR
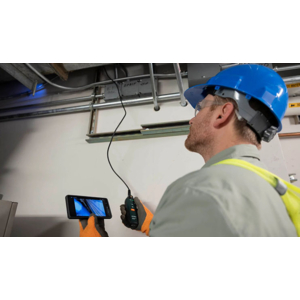
Endoscopes vidéo sans fil BR450W
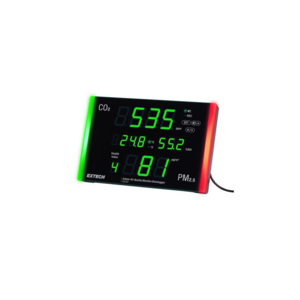
Moniteur de qualité de l'air IAQ320
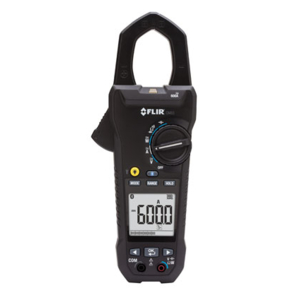
Pince de puissance CM83
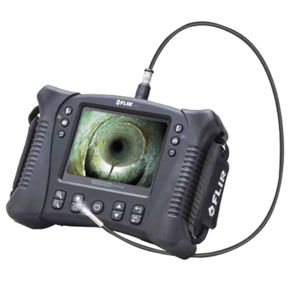
Vidéoscope FLIR VS70
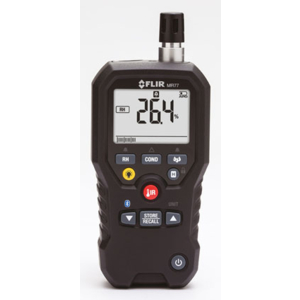