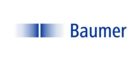
Des codeurs HeavyDuty pour les applications de grues et de levage
02/06/2020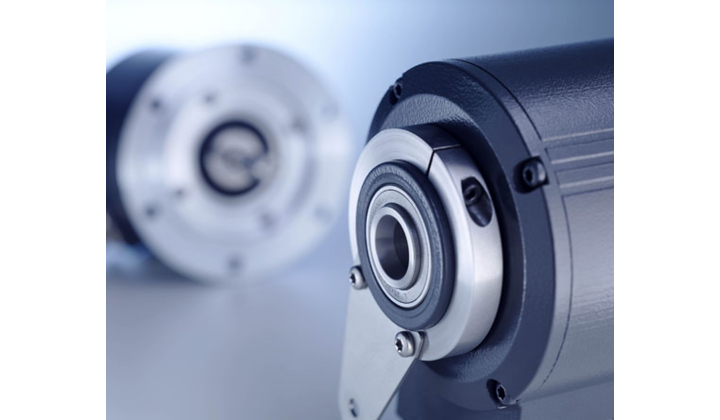
Les codeurs HeavyDuty offrent aux utilisateurs de grues et d’engins de levage le contrôle nécessaire pour lever et positionner des charges de plusieurs tonnes rapidement, efficacement et avec une précision millimétrique, et ce dans les conditions les plus difficiles, de manière fiable, pendant de nombreuses années et sans perte de précision.
Les grues sont en quelque sorte les éléphants du règne animal des machines : elles-mêmes poids lourds, elles doivent également effectuer jour après jour des travaux difficiles dans des conditions souvent peu propices. Elles sont en effet exposées à la poussière sur les chantiers et luttent contre l’eau salée et le vent dans les ports. Elles sont à la merci des intempéries et fonctionnent aussi bien en pleine canicule que par des températures glaciales. Comme dans la nature, les moins coriaces n’ont aucune chance de survivre. Les composants, tels que les détecteurs qui surveillent les vitesses et les positions angulaires des entraînements ou des axes de machine, appelés « codeurs », sont également concernés. C’est pour cette raison que les codeurs HeavyDuty sont installés dans de nombreux engins de levage et grues de grandes taille.
HeavyDuty signifie « hautement résistant ». Dans le cas des codeurs, le terme HeavyDuty n’est pas uniquement synonyme de parois épaisses et d’une protection contre la rouille, mais également une promesse de performance sur toute la ligne. Ces détecteurs effectuent les tâches qui leur sont confiées de manière fiable, sur une longue période de temps et sans jamais décevoir l’utilisateur. Cette promesse de performance est associée à des exigences très spécifiques qu’un codeur doit remplir pour pouvoir porter l’appellation « HeavyDuty ».
Quelles sont les caractéristiques d’un codeur HeavyDuty ?
Les codeurs situés sur les grues et les engins de levage lourds doivent résister pendant de nombreuses années aux chocs violents, aux vibrations ou aux forces exercées sur l’axe rotatif sans pour autant faire l’impasse sur la fonctionnalité. La robustesse mécanique est donc un facteur central : un boîtier robuste avec des parois épaisses est bien entendu un bon début, mais cela n’est pas suffisant. Des roulements massifs espacés au maximum aux deux extrémités du boîtier doivent compenser les forces axiales et radiales, et tout l’intérieur doit être conçu de manière à résister aux chocs et aux vibrations. Les codeurs HeavyDuty doivent également être insensibles aux champs électromagnétiques tels que ceux émis par des câbles sous tension non blindés. Un blindage approprié de l’électronique dans le codeur a pour objectif de la protéger de tout choc fatal et d’empêcher les signaux de mesure défectueux. Une isolation électrique est nécessaire pour résister aux éventuels passages de courant à travers l’axe, qui risquent de brûler la lubrification du roulement et d’entraîner sa destruction.
L’étanchéité représente une autre caractéristique importante. Les codeurs HeavyDuty étant souvent utilisés dans des milieux poussiéreux, sales et humides, les points névralgique, à savoir l’axe et le raccordement électrique, doivent être étanches. Une bonne protection contre la corrosion due à l’eau salée ou aux produits chimiques doit également être assurée. Enfin, un codeur HeavyDuty doit être aussi précis qu’un « petit » détecteur industriel - après tout, son rôle est de faire fonctionner avec précision les entraînements et les générateurs. Une débit fiable de signaux précis est requise : la moindre erreur peut avoir des conséquences graves et potentiellement mortelles, par exemple lors de la pose d’une charge pesant plusieurs tonnes.
Un raccordement absolu, incrémental et flexible
Une question est fondamentale pour la sélection du codeur adapté : l’application exige-t-elle l’utilisation d’un codeur incrémental ou absolu ? Baumer Hübner propose un large éventail d’options pour les deux variantes, comprenant par exemple les codeurs incrémentaux HOG 10 / POG 10, dont la réputation en matière de fiabilité sur les grues n’est plus à faire et généralement considérés comme la référence en matière de codeurs HeavyDuty. La gamme inclut également les codeurs absolus HMG 10 / PMG 10, qui prennent de plus en plus d’importance dans les applications de grues car ils sont en mesure de transmettre une position exacte, par exemple via Profinet. Étant donné que des signaux incrémentaux sont également requis pour la régulation de la vitesse à l’aide de codeurs absolus, les codeurs HeavyDuty absolus indiquent non seulement la position absolue, mais également la position incrémentale, par exemple sous forme de signal HTL ou TTL, via des interfaces numériques de série telles que SSI ou des bus de terrain. Certaines versions sont également équipées d’un commutateur de vitesse qui signale une vitesse limite via une sortie de commutation.
Différentes options de montage sont disponibles, de l’axe creux (ouvert ou ouvert d’un côté) à l’axe conique en passant par l’axe plein avec possibilité de fixation par bride EURO B10. Si nécessaire, il est possible de combiner les codeurs HeavyDuty, les commutateurs de vitesse et les dynamos tachymétriques pour former une unité robuste et peu encombrante afin de recevoir simultanément une grande variété de signaux de sortie sur un axe d’entraînement. Les grands codeurs tels que les HOG 16 / 22 / 28 de Baumer sont utilisés lorsqu’une surveillance de la vitesse des entraînements à puissance maximale est demandée ou dans des conditions très difficiles telles qu’une exposition à la poussière de charbon, l’air marin salin ou la chaleur incandescente d’une aciérie.
Autres actualités Baumer SAS
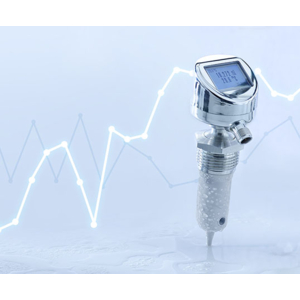
Capteur de conductivité compact PAC50
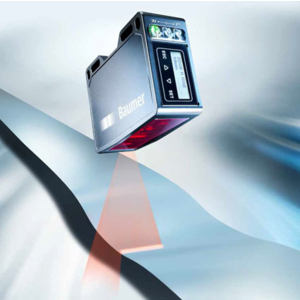
Détecteur de bord PosCon 3D
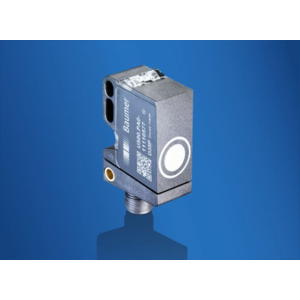
Détecteur à ultrasons U500
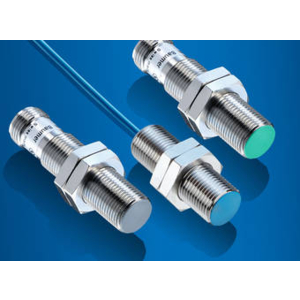
Nouveaux détecteurs inductifs ATEX

Détecteur de fuites FODK 23
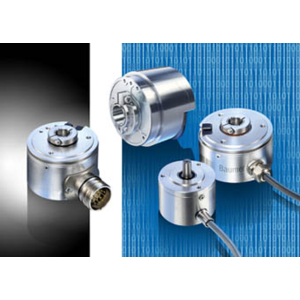
Codeurs incrémentaux programmables
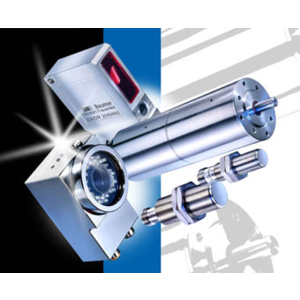
Nouvelle génération de détecteurs Inox
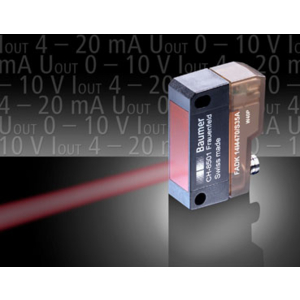
Détecteur de mesure lumière rouge
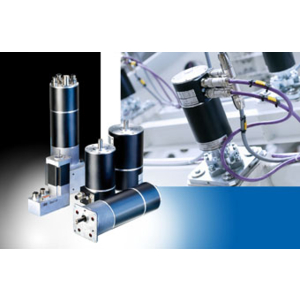
Unités d’entraînement FlexiDrive
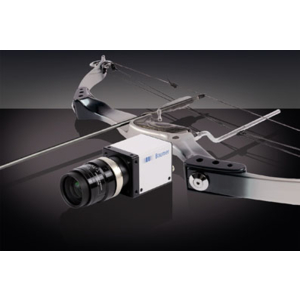