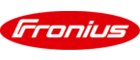
Souder un onduleur extérieur pour le rendre résistant aux intempéries
18/07/2022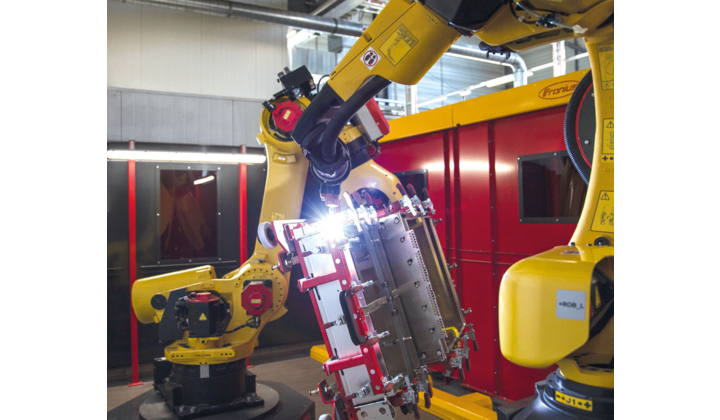
Soudé sur tout son pourtour grâce à un système de soudage robotisé Handlingto-Welding de dernière génération et destiné à une utilisation commerciale en plein air, le Tauro, dernier onduleur en date, résiste à toutes les conditions météorologiques.
Équipé d’un boîtier à double paroi et à refroidissement actif, il peut être utilisé en plein air. Pluie, fortes chaleurs ou rayonnement solaire direct : l’onduleur résiste à tout et accompli l’ensemble de ses tâches. Conçu par des experts en photovoltaïque tournés vers l’avenir, il satisfait aux exigences de l’indice de protection international IP65. Les appareils high-tech de ce type sont protégés contre les contacts, les jets d’eau sous n’importe quel angle et la pénétration de poussières. « Le soudage du boîtier en aluminium présente de nombreux défis en raison des tôles de différentes épaisseurs » explique Jasmin Gross, de chez Fronius Solar Energy. « Avec FroniusWelding Automation, nous avons trouvé le partenaire parfait directement chez nous. »
Première étape : la simulation
L’onduleur est produit sur le site autrichien de Sattledt. Spécialement conçue à cet effet, une cellule de soudage robotisée « Handling-to-Welding » ultra-moderne soude le boîtier et les portes. « Nous programmons et simulons l’ensemble des déplacements du robot et des séquences de soudage hors ligne, à l’aide du Fronius Pathfinder, c’est-à-dire sur un jumeau numérique séparé de l’installation » explique Anton Leithenmair, responsable de Welding Automation. « Ainsi, nous détectons au préalable les éventuels éléments encombrants et les limites d’axes et définissons les réglages de la torche de soudage. Nous pouvons intervenir à temps, et pas uniquement pendant les premiers essais de soudage. Une fois les séquences de soudage programmées, Pathfinder transmet les données au post-processeur, qui les traduit dans la langue du robot Fanuc. Cela nous permet de réaliser des économies considérables de temps et d’argent. La programmation hors ligne raccourcit de plusieurs heures l’apprentissage par le robot dans la cellule de soudage ! »
Planification du flux de travail à la minute près
Avant le début de la production, les commandes de Tauro sont créées dans un système ERP(Enterprise Resource Planning). Elles constituent la base de la planification des ressources de fabrication (MRP). Lors de ce processus, toutes les commandes de production sont créées pour les boîtiers et les portes. Puis, une date de production est attribuée à chaque commande. La planification détaillée qui suit est réalisée grâce au logiciel de pilotage de la production (MES).Chaque commande y est planifiée à la minute près, et est affectée à un couloir de commande libre.
Parfaitement adapté : pointage, chargement, soudage
Le soudage du boîtier à double paroi de l’onduleur présente un véritable défi dès le départ en raison des tôles de différentes épaisseurs. « Avant d’assembler les différents éléments en tôle dans la cellule de soudage robotisée conformément aux normes, nous les pointons manuellement grâce au process MAG. Cette étape nécessite déjà un travail de précision » explique Christian Kraus, chef du département de fabrication de tôles..
Une fois les travaux de pointage terminés et comptabilisés sur le terminal de l’installation, la commande centrale du système autorise l’étape de travail suivante, à savoir le soudage robotisé. Le boîtier est ensuite placé sur le chariot, serré puis transporté dans le sas. Dès que le boîtier quitte le sas, l’installation démarre la prochaine étape : le programme de robot responsable du positionnement et du soudage est sélectionné à l’aide d’une puce RFID (Radio Frequency Identification) sur le dispositif de serrage.
« Peu importe le composant situé dans le sas, la puce RFID sait quel process de soudage doit être utilisé » ajoute Christian Kraus. « Par exemple, nous pouvons occuper le sas un avec un boîtier d’onduleur pendant que nous soudons une porte via l’alimentation en composants du sas deux, et inversement. L’utilisation de la technologie RFID nous permet de souder des composants indépendamment de leur forme, de leur taille et du nombre de pièces. Qu’il s’agisse de la taille de lot 1ou d’une production en série, rien n’arrête notre cellule de soudage robotisée Handling-to-Welding. »