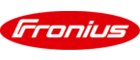
L’équipementier automobile Magna fait appel aux techniques de soudage high-tech de Fronius
27/05/2022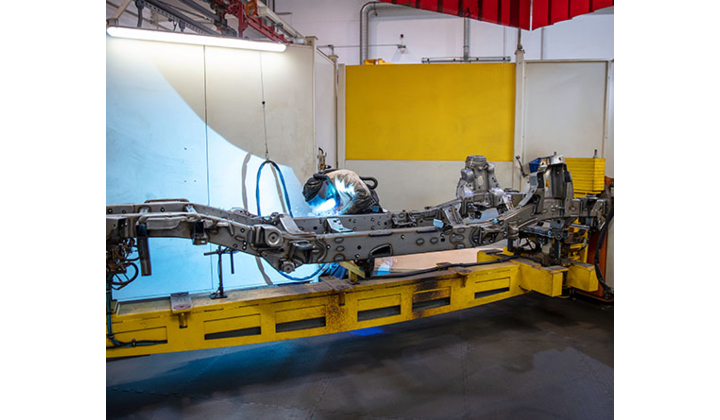
Pour assurer la qualité et optimiser ses processus de production, le groupe Magna a recours aux techniques de soudage de Fronius. Magna Presstec assemble de son côté le cadre de châssis de la Mercedes Classe G en utilisant la solution logicielle WeldCube Premium de Fronius.
Les véhicules tout-terrain high-tech nécessitent des soudures de qualité optimale
La Mercedes Classe G est considérée comme l’un des véhicules les plus adaptés à la fois au tout-terrain et au quotidien dans le monde entier. Comme on peut le deviner en voyant son énorme garde au sol et la profondeur de gué : le véhicule doit pouvoir résister aux conditions tout-terrain les plus difficiles.
La Mercedes Classe G doit présenter une force de traction et une durabilité à toute épreuve pour pouvoir être soumise à des chocs violents à grande vitesse sur des terrains accidentés, comme lors des tests continus de longue durée sur le terrain escarpé du Schöckl près de Graz. En effet, les véhicules sont testés sous toutes leurs coutures sur un circuit de montagne spectaculaire, c’est pourquoi la construction du cadre de châssis de la Mercedes Classe G doit faire l’objet d’une attention totale. Et il va donc de soi que la qualité des soudures doit également répondre aux exigences les plus élevées.
Exigences de la Mercedes Classe G en matière de soudage
« L’acier est majoritairement utilisé sous forme de tôles d’une épaisseur de 2 à 4 millimètres, assemblées au moyen de 657 soudures. La longueur totale des soudures est de 76 mètres par cadre. Pour nous, le défi du soudage consiste essentiellement à construire le cadre de châssis de 4,2 mètres de long, couche par couche, en respectant toujours les tolérances imposées par le client et la qualité de pointe requise, »explique Kurt Hartmann.
Par conséquent, l’équipement de l’installation de production devait répondre à différentes exigences en matière de technique d’assemblage : une grande stabilité de l’arc électrique avec une pénétration parfaite était nécessaire pour pouvoir générer la stabilité indispensable du cadre de châssis massif. La qualité supérieure du produit exige en outre une déformation aussi faible que possible et un apport d’énergie contrôlable. En ce qui concerne la productivité, il fallait également pouvoir atteindre des vitesses de soudage élevées.
« Le process PMC (Pulse Multi Control) de Fronius est celui qui répondait le plus à nos exigences »,assure M. Hartmann, lui-même expert international en soudage.« Pour cela, il nous fallait la plateforme de soudage modulaire TPS 500i. Son utilisation devait être simple et nous devions pouvoir la connecter aisément au robot. Actuellement, nous avons 36 de ces systèmes de soudage en service sur la ligne de production de la Mercedes G. En outre, quelques systèmes TPS 320i sont utilisés pour d’éventuels travaux de soudage manuel à des fins de contrôle qualité ».
Production de pointe autonome en detail
« Chaque cadre doit être absolument identique, tout écart est exclu »,explique M. Hartmann. La production se déroule dans un hall d’usine de plus de 100 mètres de long, parfaitement équipé. En grande partie autonome, elle répond aux normes les plus strictes et les systèmes robotisés, parfaitement adaptés, fonctionnent parfaitement les uns avec les autres. Il est ainsi possible de voir un cadre de châssis de Mercedes Classe G, robuste et parfaitement assemblé à partir de nombreuses pièces, quitter l’atelier toutes les 10 minutes.
La fabrication se déroule en trois étapes : les structures avant et arrière sont produites simultanément. Quelques collaborateurs commencent par équiper les dispositifs de soudage. Les composants sont ensuite assemblés dans les cellules à l’aide de robots de soudage. Un robot de manutention prend les composants finis, les transporte vers la cellule suivante et les positionne. À la fin de chaque section se trouve une cellule inaccessible aux collaborateurs. Celle-ci sert non seulement à souder les longues soudures, mais elle est également utilisée comme station de refroidissement ou comme station complexe, par exemple pour le « squeezing » : étape dans laquelle les coques inférieures sont alors emboîtées avec les coques supérieures des longerons, mises en position et soudées sous pression.
C’est dans le soubassement, soit à la dernière étape de fabrication, que les parties avant et arrière sont finalement assemblées. Le cadre de châssis prend alors sa forme caractéristique. Les dernières étapes de travail comprennent ensuite le poinçonnage des points d’ancrage découplés pour le châssis et le soudage par arc tiré de 192 goujons sur le cadre. Enfin, la qualité des soudures est contrôlée, les éventuelles projections de soudure sont éliminées et, le cas échéant, les soudures sont retouchées. Pour finir, une technique laser robotisée mesure à nouveau le cadre de châssis avec précision et vérifie qu’il répond à tous les critères de qualité.
Gestion ultra professionnelle des données numériques de soudage
Le processus extrêmement complexe le prouve : chez Magna Presstec, il ne s’agit pas seulement de soudage. Afin de pouvoir garantir un haut degré d’automatisation et une qualité tout aussi élevée pour la ligne de production de la Mercedes Classe G, l’accent a été mis dès le départ sur l’intégration d’outils de surveillance et d’analyse des données de soudage. L’équipementier automobile a cherché à collaborer avec des spécialistes des techniques d’assemblage dont les systèmes et les solutions permettent une traçabilité numérique totale des processus de soudage.
Avec la solution logicielle WeldCube Premium, Fronius a réussi pour la première fois à intégrer un système complet de gestion des données numériques de soudage dans l’installation de production d’un fournisseur automobile de premier rang et à démontrer l’utilité des différents systèmes logiciels utilisés.
De l’assurance qualité à la maintenance prédictive :
les solutions logicielles WELDCUBE PREMIUM et CENTRAL USER MANAGEMENT
« Fronius est un excellent partenaire »,assure Kurt Hartmann. « WeldCube Premium est un pilier essentiel de notre gestion de la qualité. Il est très important pour nous de pouvoir assurer la traçabilité de chaque soudure.» Aux postes de contrôle de la qualité, les collaborateurs formés reçoivent des informations très précises via un terminal : y a-t-il des soudures suspectes ou réellement défectueuses ? Les endroits sondés avec Fronius WeldCube sont soumis à un contrôle visuel détaillé et, le cas échéant, retravaillés. Ce n’est qu’ensuite que le cadre de châssis est envoyé vers les autres étapes du processus. Les données collectées sont alors à leur tour intégrées dans l’optimisation des process de soudage automatisés. WeldCube Premium enregistre chaque millimètre de soudure. Ainsi, il est aisé d’analyser les dépenses en consommables tels que le gaz et le fil d’apport. Mais la solution possède un potentiel encore plus grand : la maintenance prédictive par exemple, soit la possibilité de commander des pièces d’usure et des matériaux à temps et en quantité suffisante.
« La maintenance prédictive permise par WeldCube Premium pourrait présenter un potentiel d’économie, par exemple si le système de gestion des données de soudage fixait des intervalles de maintenance précis »,imagine M. Hartmann.« Nous serions toujours au courant de l’état des tubes contact, des cols de cygne, des torches et des dévidoirs. Nous pourrions ainsi les entretenir à temps afin d’éviter les soudures défectueuses, les retouches ou même les rebuts. »
Magna Presstec utilise en plus déjà la solution Fronius Central User Management (CENTRUM) qui l’assiste également en matière de gestion de la qualité. La solution permet de gérer de façon centralisée les autorisations d’utilisateur et de soudage. Le soudeur s’identifie sur l’installation de soudage à l’aide d’une carte à puce, ce qui garantit que seuls les collaborateurs ayant reçu une formation spécifique peuvent travailler avec les paramètres prévus, ce qui permet d’éliminer au maximum les sources d’erreur.
Magna Presstec prouve que la gestion des données de soudage est une solution pratique
Le responsable grands comptes de Fronius pour Magna, Christoph Pangerl, est sûr de lui :« Les enseignements tirés de la coopération avec Magna Presstec ont été extrêmement précieux. Nous avons pu les intégrer directement dans le développement de nos produits et avons ainsi rendu nos solutions logicielles accessibles à un large cercle de clients. »Kurt Hartmann poursuit :« La gestion des données de soudage en particulier, nous aide à optimiser notre technique d’assemblage dans tous les domaines. Fronius nous a fourni un outil vraiment performant. Le potentiel est énorme. Et grâce au soutien technique des experts de Fronius, ce système nous est désormais très profitable. »