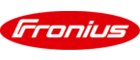
Le soudage LaserHybrid fait ses preuves sur les profilés extrudés
26/02/2020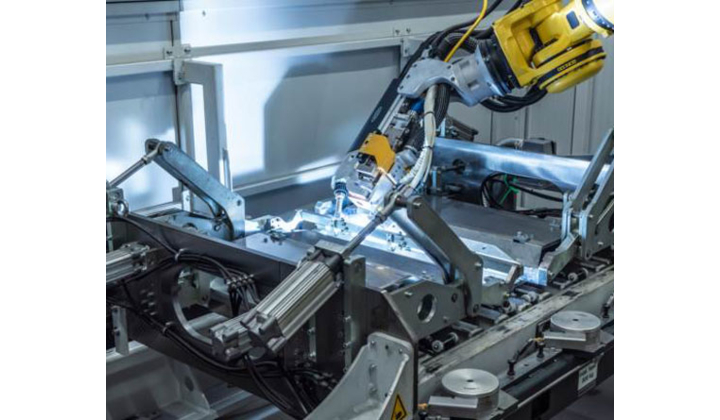
Pour le soudage de ses profilés extrudés, le fournisseur automobile Alu Menziken mise sur le procédé de soudage LaserHybrid de Fronius, qui offre des avantages considérables par rapport au, très répandu, soudage par friction-malaxage, les excédents de matière ne sont pas un problème et il permet de réaliser aussi bien des soudures d’angle que des soudures bout à bout.
C’est pour cette raison qu’Alu Menziken a investi dans une installation de soudage LaserHybrid pour la production de composants de carters de batteries. Avec la technologie de soudage et robotisée de Fronius Welding Automation et Fanuc, les avantages de ce process sont considérables.
Basée à Ranshofen, en Haute-Autriche, Alu Menziken Euromotive GmbH a été fondée en novembre 2014 comme filiale à part entière de l’entreprise suisse Alu Menziken Extrusions AG. L’entreprise emploie environ 700 personnes, dont 150 à Ranshofen, où elle produit des composants modernes de constructions légères et de systèmes en aluminium pour l’industrie automobile et aéronautique. Dans le secteur automobile, les autrichiens se sont imposés en tant que fournisseur des grands constructeurs, des constructeurs de voitures de sport et du domaine de l’e-mobilité. Les composants et modules habituels sont les systèmes anti-collision, les structures de siège, les systèmes anti-retournement et les carters de batterie.
Outre l’expérience, la flexibilité et les compétences d’Alu Menziken en matière de développement, les constructeurs automobiles apprécient notamment son intégration verticale et son vaste savoir-faire dans le domaine de la production. Avant l’apparition des prototypes d’éléments de carters de batteries, tous les croquis de construction sont contrôlés pour s’assurer qu’ils sont réalisables, puis le déroulement du processus est simulé. Les contrôles portent sur la comptabilité de toutes les pièces avec soudage et assemblage et, si besoin, des corrections sont proposées, comme l’augmentation d’un rayon ou la modification d’un talon.
Priorité absolue : l’étanchéité des carters de batteries
Le secteur automobile exige des résultats de soudage quasiment plans et sans déformations. En parallèle, les composants sont de plus en plus grands et difficiles à souder avec une qualité reproductible. Avant que les carters de batteries ne soient ajustés au millimètre près dans les châssis des véhicules, ils doivent être soumis à un contrôle d’étanchéité. La raison : tous les carters de batteries doivent être étanches à l’air, mais aussi protégés contre les projections d’eau, ce qui fait du soudage un véritable défi.
Le soudage de l’aluminium est particulièrement contraignant en raison des exigences élevées en ce qui concerne l’état de surface, la conductivité thermique ou la propreté. Cela nécessite non seulement une connaissance approfondie en matière de préparation des soudures ou de réglage des paramètres de soudage, mais également de connaître le bon ordre des étapes de soudage permettant d’éviter que les différents éléments du carter ne se déforment. Alu Menziken possède ces connaissances spécifiques. L’entreprise porte la certification EN ISO 3834-2 TÜV et emploie, outre des experts de soudage qualifiés, du personnel externe de coordination en soudage qui constitue une partie essentielle de son système de gestion de la qualité. Les soudages portent principalement sur des alliages d’aluminium de la série 5000-7000.
Les avantages de LaserHybrid avec les profilés extrudés
A ce jour, l’industrie automobile privilégie encore le soudage par friction-malaxage. Ce procédé ne consomme ni gaz ni matériau d’apport, et permet de souder presque sans déformations, grâce aux températures relativement faibles (environ 550 degrés Celsius pour l’aluminium). Lors de ce process, un outil en rotation (appelé « pin ») pénètre au niveau du plan de joint avec une force élevée. Il réchauffe la zone à souder en quelques secondes, jusqu’à lui faire presque atteindre le point de fusion. Dès que le matériau commence à ramollir, le pin commence à se déplacer vers l’avant et à tourner le long de la ligne d’assemblage avec une grande force d’appui. L’aluminium qui fond autour du pin s’assemble, pour former finalement une liaison de matière à matière.
Pour finir, l’avance s’arrête et l’outil en rotation est retiré de la zone à souder. Mais c’est précisément ce mouvement qui présente un inconvénient considérable du soudage par friction-malaxage : un trou se forme à l’endroit où l’outil en rotation quitte le matériau de base. Le constructeur doit prévoir de retirer ce « dépassement de la pièce » après le soudage. Autre inconvénient : le process Friction Stir Welding ne convient pas à la réalisation de soudures d’angle. Les soudures d’angle et bout à bout nécessitent toujours deux étapes de travail séparées car elles ne peuvent pas être réalisées avec la même tête de soudage, ce qui est en revanche possible avec le soudage LaserHybrid en position PA et PB.
Pour Alu Menziken, l’avenir s’appelle LaserHybrid
Alu Menziken mise tout sur le soudage LaserHybrid. Ce procédé permet de réaliser des soudures d’angle et d’éviter les zones de sortie inutiles. LaserHybrid combine un faisceau laser avec un process de soudage MIG dans une même zone de process. Le rayon laser, très puissant et orienté sur la soudure, possède une densité d’énergie très élevée. L’aluminium s’évapore et pénètre profondément dans le matériau de base. Le process MIG qui suit le laser sert à remplir la soudure et crée une zone de liaison optimale. La chaleur supplémentaire apportée donne au matériau le temps de laisser échapper le gaz, évitant ainsi l’apparition de porosités, contrairement au soudage au laser seul.
Norbert Dickinger, responsable de production chez Alu Menziken à Ranshofen, connaît ces avantages : « Nous pouvons souder plusieurs composants de carters de batteries en une seule phase de travail, et nous augmentons notre rendement grâce à des vitesses de soudage élevées, grâce à l’arc électrique stabilisé par le laser. En même temps, l’énergie linéaire réduite permet d’éviter la déformation des composants. »
La technologie de soudage et robotisée de Fronius et Fanuc
Ce projet a été conçu en partenariat : les machines et la technologie de soudage ont été fournies par Fronius Welding Automation, les robots et le laser à fibre par Fanuc. Alu Menziken avait déjà eu l’occasion de se faire une bonne image de Fronius à plusieurs reprises, car l’entreprise utilise depuis longtemps des sources de courant de soudage des séries TPS et TPS/i pour le soudage manuel et robotisé.
« Fronius nous a séduits par son support exemplaire. Lorsque l’on a besoin d’aide, quelqu’un arrive rapidement. Nous résolvons les petits problèmes avec l’aide du support téléphonique ou de la maintenance à distance. Par ailleurs, Fronius propose régulièrement des cours de formation continue pour les techniciens de soudage. Le bon climat d’entreprise joue également un rôle important. À tout cela s’ajoute le fait que les appareils Fronius ne tombent presque jamais en panne, car tous les composants intégrés sont d’excellente qualité », se réjouit Sven Esterbauer, ingénieur spécialisé en soudage chez Alu Menziken. Norbert Dickinger appuie les propos de son collègue : « Sur ce projet également, Fronius nous a apporté un support sans faille. »
Avant que la nouvelle cellule de soudage robotisé ne soit conçue, Fronius a réalisé les premiers essais de soudage à Thalheim. Lorsque les résultats ont été satisfaisants, l’installation a été mise au point et fabriquée. Ensuite, Alu Menziken a fourni un dispositif de soudage avec système de serrage à point zéro pour poursuivre les essais et déterminer les paramètres. Par la suite, la cellule de soudage robotisé a été construite à Ranshofen. « Avec Fronius, nous avons ensuite optimisé l’ensemble des paramètres. C’est comme cela que doit fonctionner une collaboration partenariale », ajoute M. Dickinger.
Pour l’automatisation de l’installation de soudage, Alu Menziken s’est tourné sans hésiter vers Fanuc : ce spécialiste a fourni le robot, mais aussi la source laser. Un avantage qui se ressent dans la synchronisation optimale de la vitesse du robot et de la puissance du laser. D’autres atouts : la convivialité et la simplicité de programmation du robot.
Adapté à différentes tailles de composants
Différentes pièces en profilés extrudés peuvent être soudées jusqu’à une certaine taille de module. La zone de soudage mesure 2 800 x 2 000 millimètres, et le poids de composant par côté du positionneur est de 500 kilogrammes.
Le processus de fabrication est partiellement automatisé : une fois que l’ouvrier a placé les composants en aluminium sur un positionneur, il active le processus de serrage automatique, sécurisé par une barrière immatérielle. Ensuite, le positionneur pivote vers la cabine de protection laser et le robot de soudage se déplace vers sa position initiale. Le programme de soudage se déroule automatiquement, tout comme le nettoyage de la torche selon des cycles programmés. Une fois l’opération terminée, le robot passe en position d’attente et le positionneur fait tourner le composant soudé pour le faire sortir de la cabine. Enfin, la pièce est desserrée automatiquement et peut être retirée.
Pour Sven Esterbauer, cette installation offre des avantages majeurs : « La commande de système Fronius est si intuitive qu’un nouvel utilisateur est capable de commander l’installation en quelques minutes. Grâce au large écran tactile, on a toujours un aperçu du processus dans son intégralité, y compris sur la position du robot, les paramètres de process et le suivi des soudures. »
Laser-Hybrid : plus économique, plus rapide, plus flexible
Alu Menziken Euromotive est convaincue des avantages du procédé LaserHybrid. L’entreprise peut désormais réaliser des soudures d’angle et bout à bout, et souder des composants complets en une seule phase de travail, ce qui rend le process plus rapide et plus économique.
« Je suis certain qu’Alu Menziken va établir le procédé LaserHybrid dans l’industrie automobile », déclare Norbert Dickinger. Pour argumenter son propos, le fournisseur a assemblé un équipement spécial à des fins de démonstration, à partir de différents composants, avec des épaisseurs et des profondeurs de pénétration variées, ainsi que des coupes macroscopiques d'échantillons de soudure. « La nouvelle cellule de soudage robotisé de Fronius Welding Automation et Fanuc nous y aidera », ajouter M. Dickinger, convaincu.