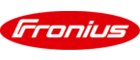
Altec, le spécialiste des solutions d’échafaudage mise sur les techniques de soudage de Fronius
26/07/2021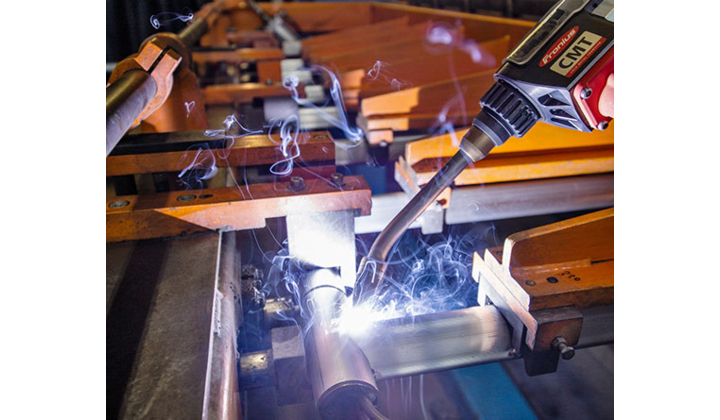
Grâce au mode opératoire de soudage CMT proposé par Fronius et à la caractéristique d’impulsion Ripple Drive, la production industrielle d’ALTEC est désormais tournée vers l’avenir.
Incarnation de la dynamique, l’aluminium permet de repousser les limites dans le secteur de la construction légère automobile tout comme dans l’industrie aérospatiale. Il simplifie le quotidien lorsque des constructions volumineuses doivent être déplacées, notamment à l’aide des diverses solutions de contrôle d’accès en aluminium d’ALTEC Aluminium-Technik GmbH & Co. KGaA.
Située à Mayen, en Rhénanie-Palatinat (à l’ouest de l’Allemagne), cette entreprise de taille moyenne propose une très large gamme de produits : des échafaudages roulants, échafaudages de façade et harnais de sécurité pour toit plat jusqu’aux nombreuses solutions spéciales, en passant par des installations de quai complètes. Ces solutions sont notamment utilisées dans le domaine des escaliers de maintenance mobiles, des plates-formes de travail, des sauts de loup ou des escaliers avec plate-forme pour l’industrie.
Une entreprise certifiée spécialisée dans le soudage aux techniques ultramodernes
En production, ALTEC transforme et soude jusqu’à 95 % d’aluminium. Environ 5 % concernent les applications en acier. Mais quelle que soit l’application en question, grâce à ses 35 années d’expérience dans le soudage, l’entreprise spécialisée dans le soudage de composants en aluminium, certifiée conforme aux normes EN 1090-1 et -3 et employant une cinquantaine de personnes, est capable de réaliser les commandes les plus complexes.
Utilisation des technologies de soudage de Fronius chez ALTEC
Dans le cadre de la progression de l’automatisation, une pièce spécifique de l’échafaudage en aluminium (AlSi1, deux millimètres), désormais requise en grandes quantités, devait être transférée de la fabrication manuelle au soudage robotisé. La vitesse de soudage élevée comptait parmi les conditions essentielles pour conférer un avantage concurrentiel à l’entreprise. Dans le même temps, la construction devait garantir une sécurité de process maximale.
En 2018, en tant que spécialiste d’applications sur tôles fines et sur aluminium, Fronius a su s’imposer face à la concurrence : son process CMT (Cold Metal Transfer) a été choisi par ALTEC. En effet, c’est précisément dans le secteur des tôles fines que le CMT, en combinaison avec la plate-forme de soudage de pointe TPS 320i, assure des vitesses de soudage particulièrement élevées. Par la suite, Fronius a réussi à s’imposer au sein de la production d’ALTEC.
Après 25 ans de production automatisée, d’autres secteurs des techniques de soudage robotisées d’ALTEC avaient fait leur temps. L’objectif de Siegfried Berenz, directeur des opérations, était de permettre à la production d’affronter la concurrence à l’avenir. Les expériences avec le process CMT étant positives, le spécialiste en soudage s’est une nouvelle fois adressé à l’équipe de vente et de service allemande de Fronius, située à Kaiserslautern.
Autres défis à relever pour la production d’ALTEC
Les techniques de soudage obsolètes du système concurrent entraînaient jusqu’à 70 % de travaux de retouche sur le système d’échafaudage en raison d’une augmentation constante des erreurs de soudage. Le rapport entre les coûts et le temps requis ainsi que la charge de travail n’était donc plus à l’équilibre ; le soudage robotisé ne présentait plus aucun avantage et la soudure ne répondait visuellement absolument plus aux exigences élevées d’ALTEC. Cependant, la pièce ne devant pas être produite en quantités très élevées, investir dans une installation de robots moderne ne semblait pas justifié.
Les exigences d’ALTEC étaient claires : la nouvelle installation devait garantir une compatibilité avec les techniques robotisées traditionnelles ainsi qu’une sécurité de process maximale, assurant ainsi un taux de pannes proche de zéro. Le plus grand défi à relever était la réalisation d’une soudure à pleine pénétration. En effet, en raison du style rond et de la préparation arrondie du barreau, la soudure fixe passe par une soudure montante, une soudure en gouttière et une soudure verticale en descendant. Un process adapté à tous les soudages en position était donc indispensable.
Parallèlement, un écart de deux millimètres est apparu dans la zone de la soudure en gouttière en raison de la préparation. Il était donc nécessaire que les techniques de process présentent également une capacité particulièrement élevée à combler les jeux. Enfin, pour pouvoir se démarquer nettement de la concurrence dans le secteur de la fabrication d’échafaudages, le process de soudage utilisé à l’avenir devait également s’accompagner d’un aspect de soudure le plus esthétique possible. ALTEC cherchait également des alternatives de modernisation.
Passage au Ripple Drive PMC
Des essais de soudage approfondis réalisés au centre de compétences des techniques d’application de Fronius, à Neuhof-Dorfborn, près de Fulda (en Allemagne), ont démontré que la variante de process Ripple Drive PMC, une caractéristique spécifique au soudage à l’arc pulsé, représentait la solution la plus adaptée aux défis de soudage d’ALTEC.
Le mode de fonctionnement de Ripple Drive est aussi simple qu’astucieux : des temps de pause, au cours desquels l’arc électrique est complètement à l’arrêt, sont définis entre un nombre d’impulsions déterminés par le soudeur. Ainsi, le bain de fusion a le temps de refroidir, ce qui permet de réaliser des soudages dans toutes les positions tout en garantissant facilement la capacité à combler les jeux de 2 millimètres. Le mode de fonctionnement de Ripple Drive permet également d’obtenir un aspect en vagues, tout aussi élégant que celui du soudage TIG.
Grâce aux fonctions PMC (Pulse Multi Control), il est en outre possible de déterminer le nombre, la forme et la taille de chaque point de soudure en définissant précisément les courants d’impulsion. Les caractéristiques de l’échantillon de soudure similaire au TIG peuvent donc également varier.
Compatibilité du TPSi avec tous les systèmes de robots
Seule la connexion avec le robot posait encore problème à ALTEC. La tâche consistait à combiner la nouvelle plate-forme numérique de soudage de pointe TPS 320i et la torche de soudage PushPull Fronius Robacta Drive, nécessaire pour Ripple Drive, aux techniques robotisées traditionnelles mais parfaitement fonctionnelles. ALTEC a décidé de sauter le pas, notamment en raison du grand nombre de protocoles de bus de terrain (interfaces modernes) disponibles chez Fronius, et de la possibilité de connecter le TPSi à l’aide d’une technologie d’interface numérique ou analogique conventionnelle.
Il en résulte un avantage indéniable : le TPSi est en réalité compatible avec presque tous les robots. De plus, de nombreuses interfaces matérielles et logicielles standardisées provenant de divers fabricants de robots sont créées dès le départ sur la source de courant haute technologie, ce qui permet de réduire au minimum le temps d’installation nécessaire pour intégrer la source de courant au système robotisé.
Service et expertise technique de Fronius, des atouts décisifs
Siegfried Berenz, directeur des opérations chez ALTEC, est particulièrement satisfait des résultats de soudage tout comme du service : « Les conseils des techniciens d’application Fronius spécialisés et compétents et les expériences acquises avec le nouveau mode opératoire de soudage Ripple Drive ont su nous convaincre de l’efficacité de l’installation Fronius. Nous avons ainsi pu réduire les temps de soudage d’environ 20 %. »
En effet, le robot de soudage n’a plus à se déplacer dans les deux sens à partir du centre de la soudure. « Grâce à l’utilisation de Ripple Drive, le robot d’ALTEC a pour la première fois pu souder en une seule fois, de la gauche vers la droite, dans les positions difficiles de montée et de descente. De plus, il n’y a presque plus aucune erreur de soudage, et les travaux de retouche nécessaires auparavant sont aujourd’hui quasi inexistants » précise S. Berenz. Le guidage haute précision du fil y est également pour quelque chose : du fût de fil au tube contact, tous les composants du système de soudage sont parfaitement adaptés les uns aux autres. C’est donc ainsi que le fil AlSi 5, particulièrement souple, est guidé de manière tendue sur les sept (!) mètres requis.
Temps d’arrêt réduits de près de 100 %
« Cette caractéristique ainsi que la modernisation de l’installation elle-même ont permis de réduire au minimum les temps d’arrêt. L’installation n’est quasiment jamais à l’arrêt. La stabilité élevée du procédé du système de soudage Fronius utilisé nous a donc totalement convaincus », assure le directeur des opérations.
« Toutefois, en cas de pannes du système, les techniciens de Fronius, représentés par l’équipe de vente et de service Fronius située à Kaiserslautern, sont sur place en un rien de temps grâce à la densité de l’infrastructure. Ils exécutent les travaux de maintenance et de remise en état en faisant preuve de fiabilité et de compétence. »
Techniques de process exceptionnelles pour des pièces de qualité
« Même l’aspect de l’assemblage soudé s’est considérablement amélioré, rendant le travail de finition quasiment superflu » déclare avec enthousiasme Siegfried Berenz. Selon lui, l’aspect quasi parfait du Ripple Drive TIG constitue non seulement un avantage décisif, mais aussi une condition indispensable pour mettre en avant la qualité des produits ALTEC.