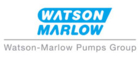
Les pompes péristaltiques APEX35 de Bredel aux États-Unis
22/07/2015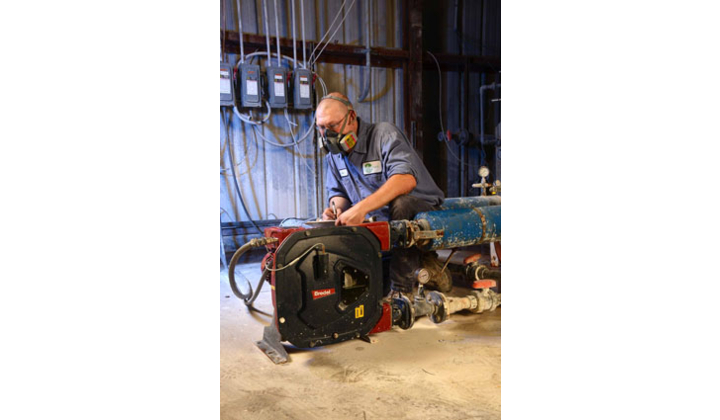
Les avantages des pompes péristaltiques APEX35 de Bredel, de Watson-Marlow Pumps Group, sont reconnus aux États-Unis, où deux usines importantes viennent d’adopter cette nouvelle technologie innovante.
L’usine texane de l’autorité régionale de l’eau et des canyons (CRWA) de New Braunfels était à la recherche d’une alternative à sa pompe à rotor excentré afin d'augmenter la précision du contrôle du pH. L'usine de traitement des eaux contrôle actuellement le pH de l’eau potable en dosant le lait de chaux à l'aide d'une pompe à rotor excentré, process qui prend environ 12 à 16 heures par jour à raison de 900 litres / heure.
Watson-Marlow a fourni une pompe péristaltique APEX35 pour essais à l'usine de New Braunfels CRWA afin que les ingénieurs puissent constater les avantages de l'utilisation d'une telle pompe pour gérer la suspension de chaux. Tout d'abord, l'uniformité insuffisante du débit de la pompe à rotor excentré tendait à engendrer des fluctuations dans le contrôle du pH, ce qui entraînait des variations de la qualité de l'eau. Avec l'installation de la pompe péristaltique APEX35 et son débit stable et constant, ces problèmes ont été éliminés.
Un autre avantage pratique de cette nouvelle pompe APEX35 sur le site est la réduction de la maintenance. La nature abrasive du lait de chaux rend nécessaire une intervention de maintenance sur la pompe à rotor excentré tous les trois mois qui peut prendre jusqu'à cinq heures. En outre, cela nécessite souvent des consommables coûteux tels que des stators, des rotors ou des garnitures. A l’inverse, la pompe APEX35 n’a exigé aucun entretien dans ses six premiers mois de fonctionnement à CRWA, et quand une intervention est finalement nécessaire, celle-ci ne prend pas plus de 30 minutes. De plus, la seule partie consommable à changer est le tube.
La réussite exceptionnelle de l'essai de la pompe APEX à la CRWA a été reproduite dans une usine du groupe Addenda, qui est en train de comparer sa pompe péristaltique existante à une nouvelle APEX35 de Bredel. La tâche consiste à transférer avec précision une boue à base de plomb contenant des solides, en suspension. La pompe péristaltique existante et la nouvelle APEX35 fonctionnent exactement dans les mêmes conditions opératoires, avec un débit d'environ 2500 litres / heure.
La pompe existante exige le remplacement du tube tous les 8 à 9 mois soit une période de disponibilité très acceptable et rentable. Le remplacement du tube des pompes APEX35 n’intervient pas avant 14 mois. Cela est en grande partie dû à la conception même de la pompe APEX, qui est optimisée pour des applications à moyenne pression et avec des tubes à durée de vie prolongée. L’augmentation du temps de disponibilité de la pompe est aussi la conséquence de la sélection de la bonne pompe pour chaque application.
Un des avantages majeurs des pompes péristaltiques APEX35 pour le transfert de substances abrasives est qu'elles ne sont pas équipées de composants coûteux à entretenir tels que les joints d’étanchéité, les soupapes, les membranes, les stators ou des rotors. Auto-amorçage, fonctionnement à sec, absence de clapets internes, la conception de la pompe APEX35 permet également aux utilisateurs d'améliorer leurs processus en éliminant les éléments auxiliaires gênants comme les clapets anti-siphonage, les clapets de contre-pression, les clapets anti-dégazage ou les protections pour le fonctionnement à sec.
Par conséquent, les pompes péristaltiques APEX35 de Bredel sont parfaitement adaptées pour le transfert et le dosage de fluides abrasifs, corrosifs, visqueux, gazeux, liquides, cristallisant, sensibles au cisaillement, ou même de fluides combinant ces propriétés.
Un autre facteur important pouvant réduire les coûts de maintenance chez Addenda est que l’Apex35 nécessite 18% de compressions de tube en moins pour le même volume transféré par rapport à la pompe péristaltique en place (qui a besoin de 1500 compressions pour 1000 litres). De plus, la technologie à montage direct et autoporté du rotor sur l’Apex permet d’optimiser la durée de vie des réducteurs et des roulements pour réduire encore les coûts de maintenance de l’usine.