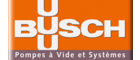
Busch installe un système de vide centralisé chez DMK
22/01/2016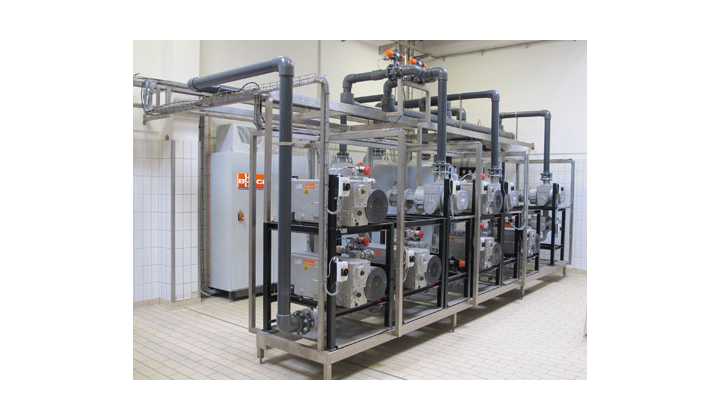
DMK Deutsches Milchkontor GmbH, un des leaders de l'industrie laitière allemande, a fait appel à Busch pour mettre en place une solution pour réduire la consommation d'énergie du système de vide qui alimente ses lignes de conditionnement et machines de thermoformage.
Les différents types de fromage en tranches destinés à la consommation sont emballés par trois machines de thermoformage sur trois lignes de conditionnement, à la fois pour DMK et pour des marques externes. Deux machines de thermoformage supplémentaires conditionnent la mozzarella en blocs de 2,5 kg et 10 kg pour transformation ultérieure par les clients.
DMK met en œuvre sa gestion de l'énergie dans le respect des normes ISO 50001, ce qui conduit l'entreprise à rechercher une solution pour réduire la consommation d'énergie du système de vide. A l'origine, les cinq machines de thermoformage étaient équipées de deux pompes à vide chacune : une pour former le film dans le moule et une pour extraire l'air de la chambre de conditionnement. Yvonne Gödeker, Responsable énergie chez DMK, souhaitait réduire le nombre de pompes à vide et les éloigner de la zone de production. En effet, la zone de production est climatisée et la chaleur émise par les pompes à vide provoquait une augmentation des coûts énergétiques. Elle a trouvé en Busch un partenaire compétent, qui lui a conseillé l'installation d'un système de vide centralisé. Busch a ensuite obtenu le contrat pour la conception, la fabrication, l'installation et la mise en service de ce système de vide centralisé. La mise en service du système a été réalisée le 1er octobre 2014. Après un an d'exploitation (octobre 2015), la centralisation du système de vide avait permis d'économiser près de 100 000 kW/h, réduisant ainsi les coûts d'énergie de DMK d'environ 15 000 euros.
Ces économies ont été obtenues grâce à une combinaison de plusieurs facteurs, mais surtout grâce au système de régulation du vide : seules les pompes à vide nécessaires pour répondre à la demande actuelle sont en service. Le vide est assuré par un système de tuyauterie avec trois circuits de vide :
- Vide primaire:
Plusieurs pompes à vide maintiennent un vide grossier permanent entre 30 et 40 mbar dans les réservoirs de vide et la tuyauterie. Ce vide est disponible directement au point de conditionnement afin d'évacuer l'emballage jusqu'au niveau de vide grossier. Le circuit de vide fin est ensuite activé.
- Vide fin:
Les modules de vide fin évacuent la chambre de conditionnement et le conditionnement du niveau de vide grossier jusqu'à la pression finale de l'emballage à moins de cinq mbar. Cette évacuation en deux étapes offre l'avantage de la vitesse : la pression finale est obtenue rapidement, ce qui permet de raccourcir les temps de cycle. C'est également le moyen le plus économe en énergie pour obtenir un vide inférieur à cinq mbar. Dans une unité de vide fin, les pompes à vide panda sont utilisées comme pompes booster
- Vide de formage
Ce circuit de vide est utilisé pour former la feuille plastique en plateaux. Le niveau de vide requis se situe entre 100 et 200 mbar. Un régulateur maintient le niveau de vide requis dans les trois circuits de vide en fonction de la demande créée par les différentes lignes de conditionnement. Les pompes à vide sont mises en service ou hors service selon les besoins, ce qui maintient la pression voulue dans les réservoirs sous vide.
Les trois lignes de conditionnement nécessitent rarement la vitesse de pompage maximum en même temps ; donc, en général, seules certaines des pompes à vide fonctionnent.
Dans le système de vide décentralisé, les deux pompes à vide ont été démarrées avec la machine de conditionnement et ont fonctionné en continu à pleine vitesse. Ce rendement maximum a été dimensionné afin de répondre à la demande créée par le temps de cycle le plus court et le plus grand volume de conditionnement de la machine. Le nouveau système de vide a considérablement réduit le temps de fonctionnement des différentes pompes à vide, ce qui, associé à l'évacuation en deux étapes, a permis de réaliser d'énormes économies d'énergie.
Le système de vide centralisé est situé sur un palier intermédiaire au-dessus des zones de production et de conditionnement. Le déplacement des pompes à vide installées directement sur les machines de conditionnement évite que la chaleur émise n'atteigne les machines de conditionnement et la zone de production. De plus, l'air chaud provenant des échappements des pompes à vide ne parvient pas aux salles climatisées. Ceci a réduit les besoins en refroidissement des machines-outils de conditionnement, ainsi que les coûts de climatisation.
Étant donné que le système de vide centralisé est désormais situé à l'extérieur, le personnel d'entretien n'a plus besoin d'entrer dans la zone de production. Le technicien de service peut effectuer la maintenance sans interrompre la production car le système possède une unité de vide en réserve. Le démarrage de cette unité de secours permet de déconnecter la première unité du réseau et d'effectuer les opérations de maintenance. Cela se traduit en une réduction des dépenses. En effet, il n'y a pas d'arrêt de la production et il n'est plus nécessaire de réaliser la maintenance pendant le week-end, quand les coûts sont plus élevés.
DMK a signé un contrat de service tout inclus avec Busch. Ce contrat signifie que Busch garantira le système pendant cinq ans, effectuera toutes les opérations de maintenance et prendra des mesures correctrices immédiates en cas de dysfonctionnement.
Autres actualités Busch
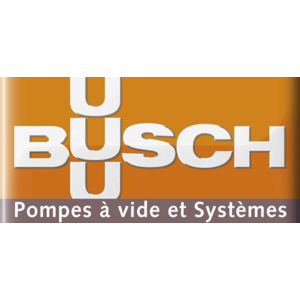
Busch présent sur le salon Chimie Lyon 2017
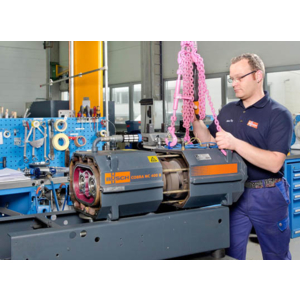
Busch s'implante en Auvergne-Rhône Alpes
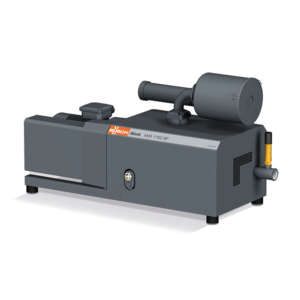
Surpresseur à becs Mink pour air et gaz
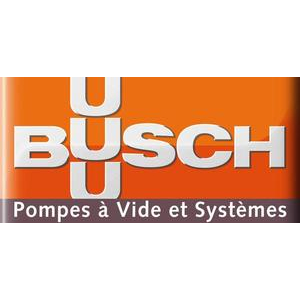
Busch au salon Ilmac 2016
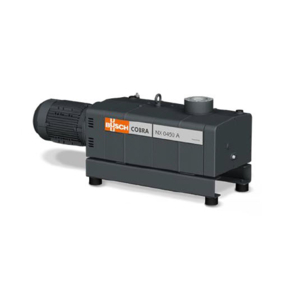
Pompe à vide sèche à vis COBRA NX 0450 A
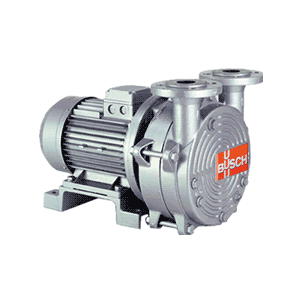
Pompes à vide à anneau liquide Dolphin
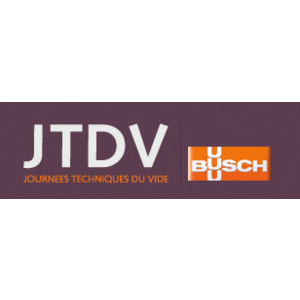
Busch lance les Journées Techniques du Vide
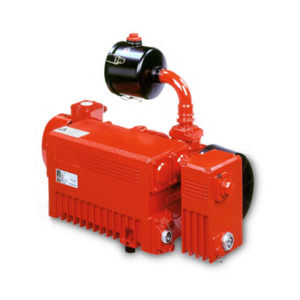
Pompe à vide R 5 version Oxygène Busch
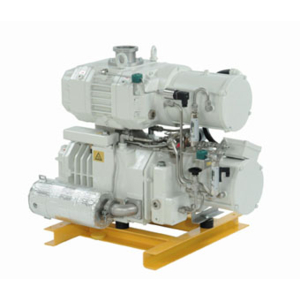
COBRA DP, la surdouée des pompes à vide
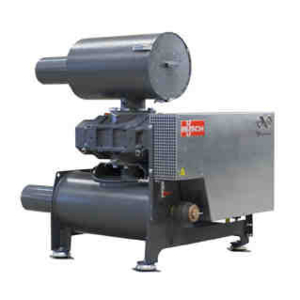
Surpresseurs à piston rotatif TYR de Busch
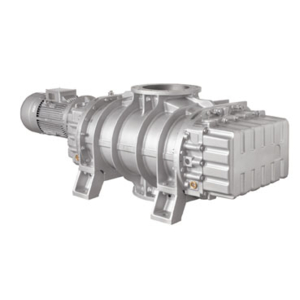
Pompe à vide sèches Roots Puma WPA 040
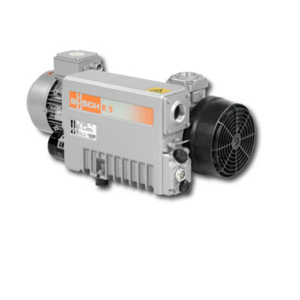
Pompes à palettes lubrifiées R 5
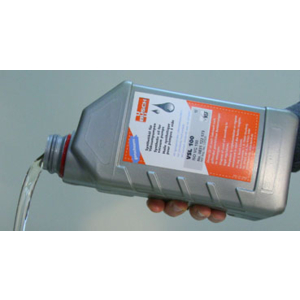
Huile VSL.100 pour pompes à vide
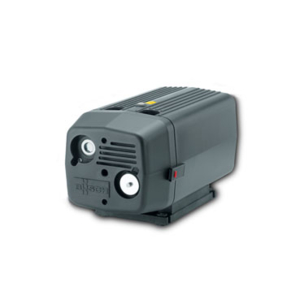
Pompe à palettes sèches Seco
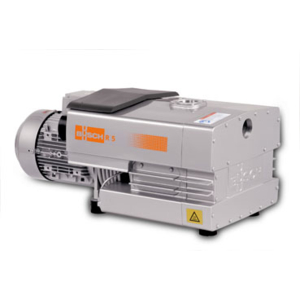