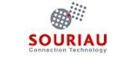
SOURIAU investit massivement dans sa R&D pour la mise en place de ses nouveaux processus de fabrication
17/10/2018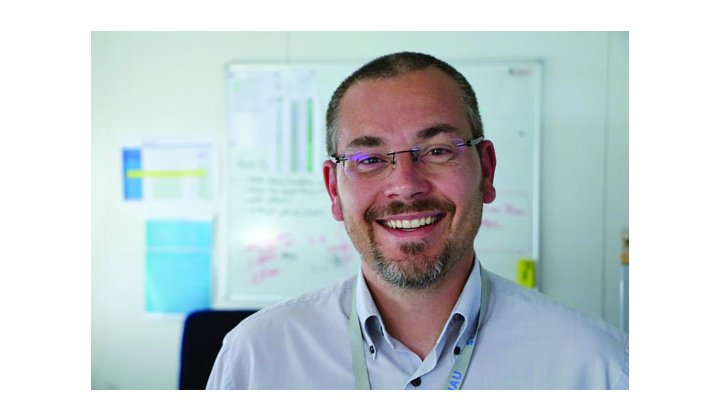
Le règlement européen REACH, qui vise à améliorer la protection de la santé et de l'environnement, impose des règles d'utilisation strictes des substances chimiques. Le chrome hexavalent, utilisé dans le traitement de surface de nombreux produits SOURIAU, fait partie de la liste des substances interdites. Désireux à la fois de conserver son leadership technique sur les produits de la connectique pour environnement sévère et d’accompagner ses clients vers plus d’innovation, le service de recherche et développement de SOURIAU investit depuis plusieurs années dans la recherche de nouveaux processus de fabrication.
Rencontre avec THOMAS PICHOT, Responsable du pôle R&D aéronautique:
Pouvez-vous nous décrire l’utilisation du chrome hexavalent dans votre métier ?
Nous concevons et fabriquons des connecteurs électriques ou optiques utilisés en environnements sévères, pour des applications spatiales, aéronautiques, militaires et industrielles. Les boîtiers et les accessoires de nos connecteurs sont en matériaux composites, en aluminium ou en acier et nous utilisons depuis des décennies le chrome hexavalent dans notre processus de galvanoplastie. Cette substance confère à nos produits des propriétés d’anticorrosion, de continuité électrique et d’aspect souhaitées par nos clients. Le chrome hexavalent étant sur la liste des substances chimiques interdites, nous travaillons à son remplacement.
Est-ce possible de remplacer un produit par un autre ?
Oui bien sûr, mais cela prend du temps. En effet, non seulement nous maîtrisons parfaitement l’utilisation du chrome hexavalent dans les traitements de différents matériaux tels que l’aluminium, les alliages de cuivre ou encore certains thermoplastiques, mais les propriétés de ce produit sont encore très supérieures à ce qu’il est possible de faire avec d’autres substances. La difficulté est donc double : s’assurer qu’il est possible de déployer le substitut industriellement, et qu’il nous permet d’atteindre les performances requises.
Par exemple : dans certains cas, nous utilisons le chrome hexavalent pour favoriser l’accroche d’autres revêtements sur le substrat. Il va donc falloir qualifier un produit qui offre la même caractéristique fonctionnelle, tout en s’assurant qu’on puisse l’inclure de manière maîtrisée dans nos procédés de fabrication. Enfin, il faut garder en tête que dans d’autres cas, le chrome hexavalent est utilisé dans les dernières étapes du processus et persiste donc en surface. Si on le substitue, il faut s’assurer de la compatibilité de nos « nouveaux » connecteurs avec les connecteurs déjà sur le terrain, puisqu’ils seront en contact.
C’est possible, mais c’est un vrai casse-tête, non ?
En fait, à ce jour, nous n'avons pas de solution de remplacement unique, parce que le chrome n'est pas utilisé pour le même besoin selon le matériau et selon le traitement final. En catégorisant nos composants de connecteurs par matières, en identifiant les mécanismes électrochimiques en jeu, et en multipliant les essais du bécher à la ligne pilote, nous avons orienté nos recherches vers des solutions multiples.
Alors où en êtes-vous de vos recherches ?
Nous n'utilisons plus de chrome hexavalent pour le traitement des boîtiers composites. Nous réalisons d’abord une opération de tribofinition pour modifier les propriétés de surface et ainsi permettre à notre nouveau traitement de préparation (sans chrome hexavalent) d'assurer l'accroche des revêtements métalliques successifs. Pour les connecteurs en aluminium, nous avons également supprimé la passivation au chrome hexavalent dans notre procédé de traitement en zinc-nickel, tout en développant un nouveau procédé utilisant une substance certifiée comme non dangereuse et autorisée par REACH. Nous avons ainsi réduit de moitié notre consommation annuelle de chrome hexavalent qui est passée de 8 à 4 tonnes.
Cette transition a-t-elle été facile ?
Evidemment non, nous avons travaillé plusieurs années pour mettre en place et valider cette nouvelle « brique technologique », car il ne suffit pas de valider un concept en laboratoire, il faut le reproduire à grande échelle et dans la durée. En quelque sorte, il faut construire une expérience. Prenez par exemple les bains de galvanoplastie, dont les volumes font jusqu'à plusieurs centaines de litres. Leur composition et leur parfaite maîtrise nécessitent de réaliser de nombreux plans d’expérience : il faut valider les temps d'immersion et les concentrations des différents produits, s’assurer de l'absence d'impact sur la géométrie des pièces, surveiller le vieillissement des bains pour garantir la qualité du traitement, etc. Des dizaines de paramètres sont à prendre en compte, à analyser et à maîtriser.
Où en êtes-vous avec le chrome hexavalent pour les connecteurs protégés en cadmium ?
A l’heure actuelle, il n'y a que la passivation au chrome hexavalent qui permet au cadmium à la fois de garantir de hautes tenues en corrosion et des performances électriques de premier ordre, tout en conservant un aspect non réfléchissant et sombre, qui reste une des caractéristiques incontournables des produits militaires. L'une des solutions qui a été développée comme alternative au dépôt de cadmium est basée sur un traitement zinc-nickel avec une passivation sans chrome hexavalent. Cela procure des propriétés de premier ordre aux produits finaux, tout en garantissant une parfaite compatibilité avec les équipements déjà installés.
Cependant, cette solution n'est pas forcément la réponse universelle. Nous continuons d’utiliser le chrome hexavalent sur des produits cadmiés pour répondre à certaines exigences de nos clients, ou pour adresser des marchés en dehors de l’Europe où la réglementation ne s’applique pas et où nous devons néanmoins rester compétitifs. Nous avons obtenu de l'Agence Européenne des Produits Chimiques une dérogation de 12 ans, que nous mettons à profit pour continuer nos recherches, tout en analysant les pratiques d'autres industries, comme l'automobile par exemple. Notre objectif final est évidemment la suppression totale du chrome hexavalent de tous nos processus de fabrication.
La transition vers la suppression du chrome hexavalent semble bien engagée…
Dès l'arrivée de la règlementation européenne REACH, la direction de SOURIAU ESTERLINE et l'ensemble des équipes ont pris conscience qu’il fallait lancer un vaste programme d'innovation des techniques de traitement de surface pour garder la production de nos connecteurs en France. C’est un effort important en termes d’investissement, qui a aussi renforcé les coopérations entre les équipes, comme avec nos clients. La volonté affichée de promouvoir notre innovation en trouvant des solutions de remplacement du chrome hexavalent renforce notre expérience et valorise nos savoir-faire. Nos clients ne s’y trompent pas : ils savent que notre démarche va dans le sens de l’histoire. Il faut protéger la santé des personnes et leur environnement.
Autres actualités Souriau
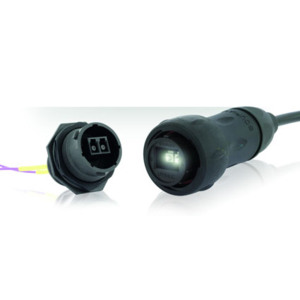
Connecteur UTS LC pour fibre optique
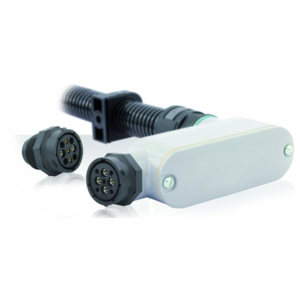
Connecteur TS threaded receptacles
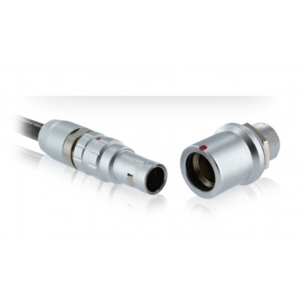
Connecteur push-pull JBX étanche IP68
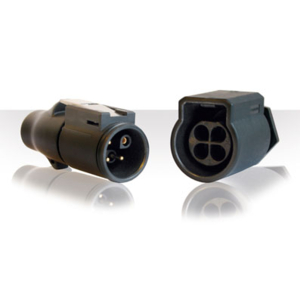
Connecteur de puissance UTL
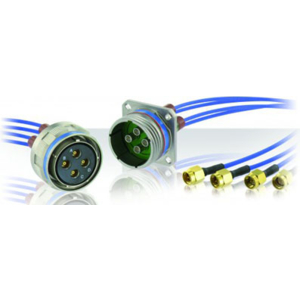
Nouveaux contacts coaxiaux RF BMA
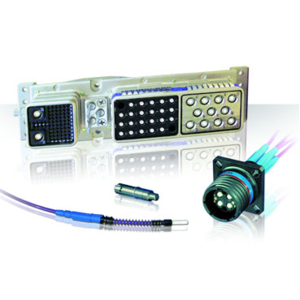