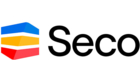
Outils pour l'arrosage sous haute pression
30/07/2013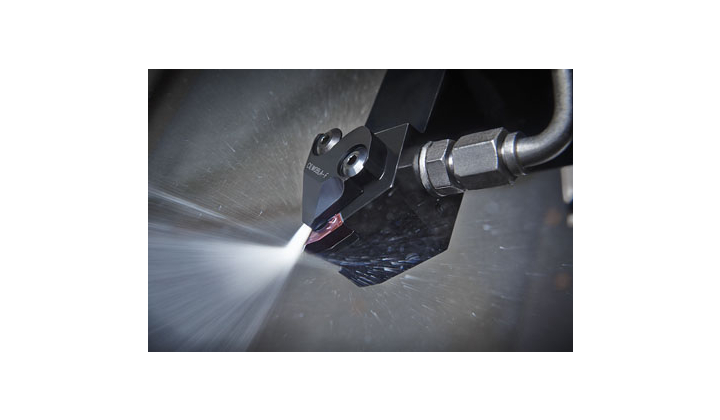
Pour surmonter les inconvénients des systèmes existants, Seco, a travaillé sur l’optimisation de la performance en améliorant la pression et la précision de la direction des flux de fluide de refroidissement sur les zones de coupe.
Les avantages liés à l'utilisation d'un fluide de refroidissement sont bien connus, le fluide de refroidissement venant généralement inonder la zone d'usinage doit réduire la chaleur et lubrifier (réduire les frottements). Toutefois, pour que le fluide de refroidissement soit vraiment efficace, il doit éliminer la chaleur de la zone de coupe, à l'endroit même où se détache la matière. Un flux de fluide de refroidissement sous haute pression, parfaitement dirigé, est beaucoup plus efficace.
Le système Jetstream Tooling® de Seco répond à toutes ces contraintes. Il dispose de buses de sortie de fluide de refroidissement disposées à des endroits stratégiques. Des brides supérieures amovibles (inducteurs) équipent les porte-plaquettes. La pression du fluide de refroidissement, le débit et les trous de petit diamètre sont les éléments qui permettent au flux d’être plus précis et plus puissant. Cela permet de pénétrer facilement dans la zone de chaleur, juste sur l'arête de coupe, et de la lubrifier.
Seco a découvert que la distribution du fluide de refroidissement par une « buse », très près de l'arête de coupe, s'avère très efficace. Cela signifie que la sortie du système dirige le flux de fluide de refroidissement entre la zone de coupe de la plaquette et le copeau, ce qui permet aussi de soulever et de fragmenter le copeau.
La dernière génération du système Jetstream Tooling® pour le tournage, les gorges et le tronçonnage est équipé de sorties de fluide de refroidissement dirigées vers les faces de coupe, mais également vers les dégagements des plaquettes, c'est-à-dire vers la zone de chaleur secondaire. Le jet de fluide de refroidissement par-dessous le copeau en formation permet un refroidissement optimal. Ce jet supplémentaire de fluide de refroidissement, dirigé vers le dégagement des plaquettes, accroît de 10 % la durée de vie de l'outil et améliore l'état de surface.
Lorsque des systèmes d'outil haute pression modernes sont utilisés par les fabricants, ils éliminent aussi les temps d'arrêt machine et obtiennent une capacité d'usinage sans problème en production. Ils peuvent aussi accroître les vitesses de coupe et les vitesses d’avance. Également allonger la durée de vie des outils et améliorer l'état de surface réalisé, le tout grâce au contrôle optimisé des flux d’arrosage et aussi de la formation des copeaux. Dans certains cas, les vitesses et les avances peuvent être triplées, et la durée de vie des outils peut également être multipliée par deux. La productivité et la rentabilité sont ainsi accrues, en usinant plus de pièces, plus vite.
Des tests en laboratoire, effectués chez Seco, sur une pièce en titane, usinée à des vitesses de coupe de l’ordre de 40 m/min (130 ft/min), une vitesse d'avance de 0,25 mm/tr (0,01 po/tr) et une profondeur de passe de 2 mm (0,08 po), avec un système d’arrosage traditionnel, sur un temps de cycle de cinq minutes. Les chercheurs ont ensuite utilisé un système d'outil à débit de fluide de refroidissement haute pression et ils sont parvenus à porter la vitesse de coupe à 80 m/min (260 ft/min) et à réduire le temps de cycle de moitié, tout en augmentant de 100 % la durée de vie des outils.
Aujourd'hui, les pompes d’arrosage qui équipent les machines-outils proposent généralement une pression comprise entre 20 bar (290 psi) et 70 bar (1 000 psi), soit une plage tout à fait adaptée au système Jetstream Tooling® de Seco. Ce système, est polyvalent puisqu'il permet à lui seul de travailler à partir de basses pressions dès 5 bar (70 psi), avec un léger impact sur la productivité, jusqu'à des pressions élevées de 70 bar (1 000 psi), voire des pressions vraiment très élevées de 350 bar (5 000 psi).
Entre 20 bar (290 psi) et 40 bar (580 psi), des gains significatifs de productivité sont relevés. Un allongement de la durée de vie et un contrôle accru des copeaux en finition peuvent être observés pour différents matériaux. Les performances augmentent en fonction de la pression et du débit (l/min). Ainsi, une pression de 70 bar (1 000 psi) suffit à fragmenter les copeaux les plus difficiles, formés dans des matériaux, augmente considérablement la durée de vie et les conditions de coupe peuvent être ainsi augmentées.
La plupart des secteurs d’activité peuvent tirer profit du refroidissement haute pression, mais ce sont traditionnellement les secteurs de l'énergie, l'aéronautique et le médical qui ont le plus recours à cette technique, du fait de leurs nombreux matériaux complexes à usiner, nécessitant une gestion intensive de la formation de copeaux.