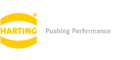
Modules électroniques sans circuits imprimés
09/09/2020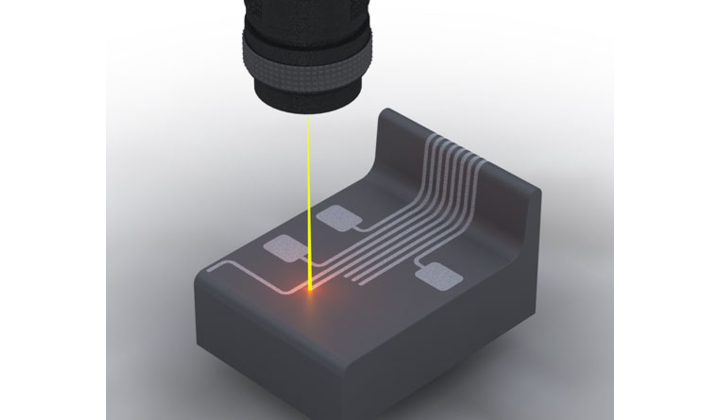
Grâce à la structuration directe au laser (LDS), il est possible d’appliquer des pistes électroniques conductrices directement à des pièces en plastique dès leur production en série. La technologie LDS permet ainsi de créer des modules électroniques aux formes géométriques flexibles.
Un procédé grâce auquel les produits électroniques tels que les smartphones, les capteurs ou les appareils médicaux deviennent de plus en plus petits et puissants. Les processus de fabrication automatisés rendent également ce procédé de plus en plus attractif d’un point de vue économique.
L’espace pour les modules électroniques étant de plus en plus exigu, on est toujours à la recherche de solutions pour remplacer les circuits imprimés classiques. LDS permet une miniaturisation supplémentaire et des conceptions géométriques toujours plus complexes. Ce processus stable et fiable s'est également imposé dans des domaines particulièrement critiques pour la qualité tels que la technologie médicale ou les composants de sécurité destinés à l'industrie automobile.
Le processus LDS permet de réaliser des modules 3D
La structuration laser directe rend possible des modules 3D-MID (Mechatronic Integrated Devices ou Systèmes intégrés mécatroniques). Avec 3D-MID, les composants électroniques peuvent être montés directement sur un corps de base tridimensionnel, sans circuits imprimés ni câbles de connexion. Le corps de base est fabriqué par un processus de moulage par injection car le matériau thermoplastique contient un additif inorganique non conducteur.
Pour que la matière plastique puisse s’intégrer dans les conducteurs électriques, les additifs dans le matériau sont « activés » par structuration directe au laser. Le faisceau laser décrit les zones destinées aux pistes conductrices ce qui crée une structure micro-rugueuse. Les particules métalliques libérées forment les noyaux pour la métallisation chimique ultérieure. Ainsi, des pistes conductrices électriques sont appliquées dans les zones marquées par le laser. Les autres zones du corps de base tridimensionnel restent inchangées. Le composant en plastique peut être assemblé ultérieurement dans des processus SMD standard comme une carte de circuit imprimé traditionnel et convient également au processus de brassage dans un four de refusion.
La technologie laser peut être utilisée de manière flexible
HARTING 3D-MID AG est le plus grand fournisseur de composants 3D-MID en dehors de l'Asie. Pour le processus LDS, HARTING utilise des systèmes laser haute performance caractérisée par trois lasers en parallèle, chacun décalé de 45 degrés. Grâce à l'axe de rotation supplémentaire, il est possible de traiter les composants par le laser à 360 degrés et de tous les côtés en même temps. Cette technologie permet de réaliser des formes géométriques flexibles, telles que des coques de réflecteur ou des lumières LED. En dépit de la faible épaisseur de la piste conductrice comprise entre 16 à 20 μm, les pistes conductrices sont adaptées aux composants automobiles exigeants ou aux applications avec des courants allant jusqu'à 10 A, telles que les bobines chauffantes dans les caméras qui empêchent l'optique de s'embuer.
HARTING est le seul fabricant de 3D-MID au monde qui dispose d'un système laser à trois optiques pour une mise au point fine de 50 μm. Grâce au laser à mise au point fine, des distances de pistes conductrices encore plus petites sont atteintes. De cette manière, un plus grand nombre de pistes conductrices peut être créé sur le même composant avec une densité de tassement plus élevée. Il est utilisé, entre autres, pour la technologie de sécurité car les pistes conductrices étroitement espacées et entrelacées déclenchent des alarmes de sécurité même avec la plus petite interférence physique.