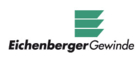
Eichenberger Gewinde a mis au point un système de réglage de siège d'avion léger et robuste
04/10/2019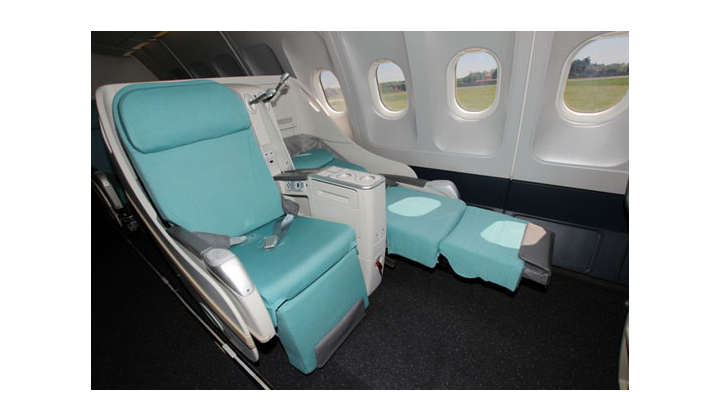
Un siège d'avion doit paraître accueillant, être confortable et très facile à utiliser. Afin de permettre aux vols d'être plus économiques et donc plus respectueux de l'environnement, le design doit se concentrer non seulement sur le confort et la fonctionnalité des sièges, mais aussi sur leur poids, l'économie d'espace, la durée de vie et la qualité. Jusqu'à présent, le réglage des repose-pieds, des assises et des dossiers des sièges d'avion était toujours effectué par trois mécanismes distincts. Avec le nouveau système de réglage, ils sont tous contrôlés à partir d'un seul point central, qui utilise trois petites vis à billes de type Carry, très précises et robustes.
Pour réduire leur consommation de kérosène, les compagnies aériennes recherchent toujours plus de solutions légères pour l'intérieur de leurs avions. De plus, pour le confort des passagers, elles souhaitent aujourd´hui proposer des sièges plus larges. Du fait des progrès technologiques, les systèmes se complexifient et il faut mettre en place des déplacements silencieux dans des espaces très réduits. Cela se traduit directement par des difficultés au niveau de l´environnement géométrique, des dimensions ainsi que des charges dynamiques et statiques des composants d´entraînement.
Selon le cahier des charges, il a fallu produire trois entraînements à vis à billes robustes et très précis. L'extérieur des écrous devait répondre à des spécifications particulières. Il a notamment fallu une très grande maîtrise pour réaliser les 10 perçages haute précision (1,52 mm de diamètre) sur la face avant des écrous des entraînements à billes, indispensables à la transmission de puissance des moteurs. Le métal « vit ». On voit très bien lors du durcissement à quel point l'acier peut être « vivant ». Au cours du procédé de durcissement, le métal se modifie différemment selon la charge et perd en précision dimensionnelle. Ces modifications ne peuvent être calculées ou prévues. Il faut donc un doigté particulier pour garantir la précision des 10 trous des écrous.
Après des cycles successifs de mesure et de durcissement, les développeurs d’Eichenberger ont réussi à ajuster les trous à la taille requise. Après un durcissement sous vide, les dimensions des trous haute précision sur l’écrou ont satisfait aux spécifications avec une tolérance de ± 0,015 mm. Les écrous ont été durcis à 59-63 HRC. En raison de l'excellente relation de travail avec la station de traitement thermique, les prototypes ont pu être fabriqués rapidement et avec souplesse. Grâce à ses processus de production intelligents, Eichenberger est en mesure de répondre aux demandes des clients très rapidement. Le calcul de la longévité d´une pièce se fait immédiatement, il est possible de l´intégrer directement dans le processus de fabrication et de s´adapter.
Au départ, notre site de production en Suisse, censément plus cher, s´est heurté au scepticisme de nos clients. Mais nos conseils professionnels, notre réalisation rapide de prototypes et notre rapport qualité-prix intéressant ont été décisifs.
Eichenberger accorde toujours la priorité au client, ce qui suppose de l´écouter, de poser des questions, de le conseiller, puis de concevoir, de tester, d´optimiser et de fabriquer des produits. Cet échange ciblé d´informations et d´idées est le seul moyen de vraiment comprendre les besoins du client et de les mettre en pratique. C´est ainsi que la société Eichenberger Gewinde AG, confiante en ses points forts, ses produits et sa chaîne de création de valeur, s´adapte à la scène internationale, qui est en constante évolution. L´expert des vis préfère « anticiper plutôt que réagir », une philosophie qui fait partie intégrante de sa culture d´entreprise. Ses entraînements à vis, fabriqués sur mesure pour ses clients, se retrouvent partout, que ce soit dans le secteur médical, électronique ou automobile, en passant par l´automatisation, l´aviation ou même l´aérospatial.