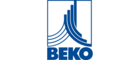
BEKO TECHNOLOGIES optimise le système de traitement d’air comprimé d’une brasserie familiale.
04/07/2024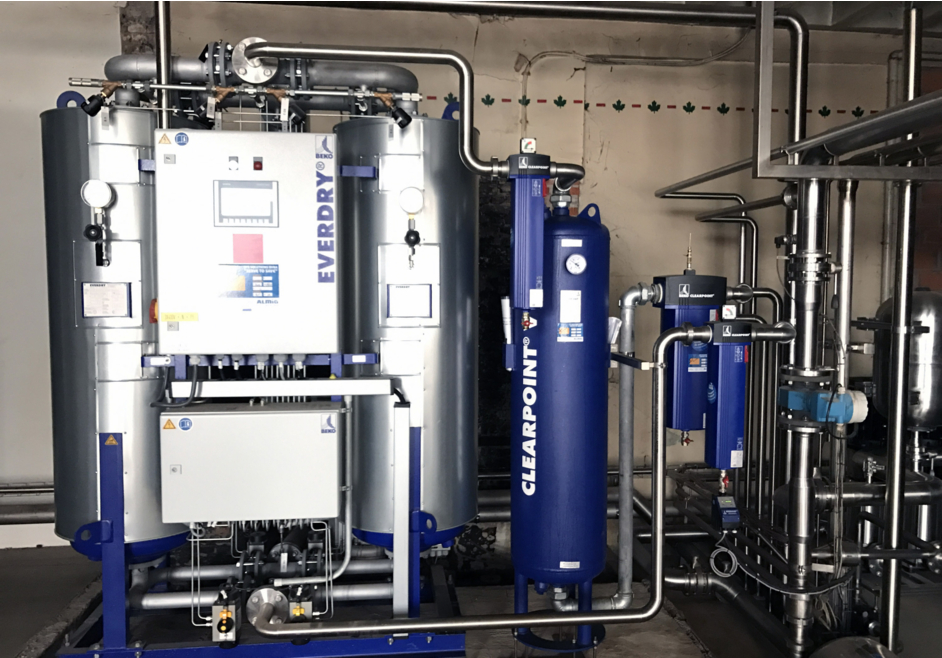
Une brasserie familiale, à la renommée mondiale, a fait appel à BEKO TECHNOLOGIES pour le traitement de son air comprimé process. Pour cette entreprise à la pointe des processus actuels, la qualité des bières produite est une priorité absolue. Pour cela, les normes élevées de qualité sont imposées à tous les fournisseurs et partenaires, que ce soit pour les matières premières, les machines ou les services de laboratoire.
Dans le processus de fabrication de la bière produite par le client de BEKO TECHNOLOGIES, l’air comprimé joue un rôle important, d’où l’attention particulière accordée à la centrale de production et de traitement d’air comprimé. Ici, l'air comprimé est utilisé pour divers processus tels que les commandes pneumatiques, les lignes de transport, le déplacement des matières premières et le soufflage de la bière hors des cuves. Si l'hygiène est moins cruciale pour la partie commandes pneumatiques, elle revêt une grande importance pour le transport et le soufflage de la bière, car l'air comprimé peut contenir des impuretés telles que de l'huile, de la poussière, de l'humidité et des bactéries, pouvant altérer la qualité du produit final.
Lors d’un échange avec un distributeur partenaire de BEKO TECHNOLOGIES, actif dans l’industrie agroalimentaire et des boissons et le responsable maintenance de la brasserie, ce dernier l’a informé du projet d’extension du site.
Au moment de l’analyse de l’installation d’air comprimé existante, notre partenaire a constaté que BEKO TECHNOLOGIES, avec ses purgeurs de condensats d’air comprimé, était déjà présent et connu par le brasseur.
La centrale de production d’air comprimé était alimentée en service continu, par deux compresseurs d’une puissance de 22 et de 15 kW.
Problèmes
Le purgeur de condensats BEKOMAT était récemment tombé en panne, d’où la nécessité de le remplacer. Le partenaire de BEKO TECHNOLOGIES précise : « ayant été contacté pour le purgeur en panne, j’en ai profité pour visiter le reste de l’installation. Au cours de ma visite, j’ai constaté que le sécheur par adsorption avec régénération sans apport de chaleur existant, rejetait de l'air en permanence, et qu'il y avait une présence d'huile et d'eau dans les conduites. Une odeur d'huile imprégnait l'air, signalant une filtration insuffisante de l'huile dans la salle des compresseurs. C'était non seulement un gaspillage d'air comprimé coûteux, mais aussi un problème de qualité. »
Il détaille : « En association avec le CO2, l'air comprimé est utilisé pour expulser la bière hors de la cuve de brassage à une pression de 1,6 bar(g). Cela signifie que l'air comprimé est en contact direct avec le produit. La présence même de traces infimes d'huile et d'eau peut altérer la qualité de la bière, créant ainsi un environnement propice à la prolifération de bactéries et d'autres organismes non souhaités. »
Solutions
Pour la partie production de l’air comprimé, les anciens compresseurs ont été remplacés par de nouveaux modèles : un nouveau compresseur à vitesse variable de 40 kW, lubrifié à l'huile, qui fonctionne en continu, associé à un compresseur stationnaire de 30 kW, utilisé pendant les périodes de pointe. La nouvelle installation se distingue par l'ajout d'un échangeur de chaleur en aval du compresseur. À l'intérieur du compresseur, la température de l'huile augmente jusqu'à environ 60-70 °C. Cette chaleur est exploitée pour chauffer l'eau provenant de la nappe phréatique, permettant ainsi la réutilisation d'une grande partie de l'énergie dans la brasserie.
Pour la partie traitement de l’air comprimé, BEKO TECHNOLOGIES a proposé une solution comportant un sécheur par adsorption commandé en fonction du point de rosée EVERDRY FRA-V 0900, équipé de préfiltres CLEARPOINT, et d'un filtre à charbon actif CLEARPOINT V, incluse une maintenance annuelle de l'installation.
Satisfaction client et évolutions de la solution
La solution préconisée et proposée par BEKO TECHNOLOGIES et son partenaire répond parfaitement aux besoins du client qui est très satisfait. Depuis lors, le système de traitement a évolué avec la proposition de deux solutions reposant sur le convertisseur catalytique pour un air comprimé exempt d’huile, de germes et de bactéries BEKOKAT, l'une destinée à être installée dans la salle des compresseurs et l'autre pour un traitement au niveau du point d'utilisation.