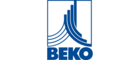
BEKO TECHNOLOGIES fournit aux Grands Chais de France une installation d’air comprimé globale
29/09/2020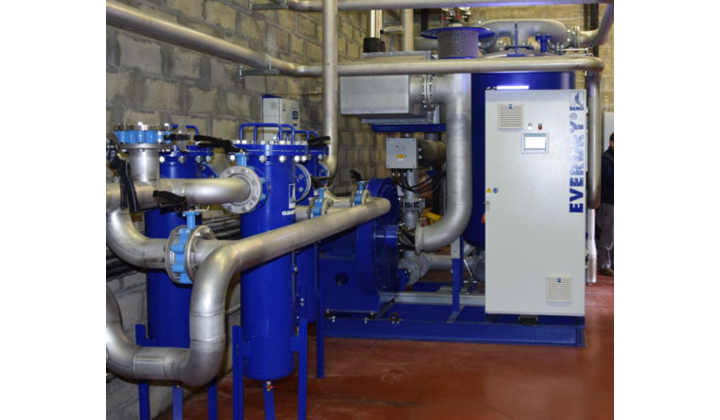
Le groupe Grands Chais de France est spécialisé dans la vinification, le négoce et l’exportation de vins et de spiritueux. À L’usine de Landiras en Gironde, qui emploie 750 salariés, des vins provenant de France et de l’étranger sont mis en bouteille pour être réexpédiés en France et à l’international. Chaque jour, un million de bouteilles de vin sortent de cette usine ultramoderne. Pour satisfaire aux exigences de son activité en termes de productivité et de sécurité alimentaire, l’expertise de BEKO TECHNOLOGIES dans le traitement de l’air comprimé a été sollicitée.
Sur le site des Grands Chais de France de Landiras, l’air comprimé est utilisé entre autres pour faire fonctionner les machines de production et comme air process (air stérile) pour pousser les vins dans la tuyauterie. Quant à l’air comprimé à 40 bar, il sert à souffler les bouteilles en PET.
Thierry Labarthe, à la fois Responsable des services généraux de l’usine bordelaise et Responsable maintenance de 15 autres sites du groupe explique : « nos machines utilisent de l’air comprimé stérile à la fois pour pousser les vins dans la tuyauterie avec des systèmes d’obus, pour sécher la tuyauterie et les bouteilles après lavage ainsi que les systèmes de filtration de vins. »
Un système de traitement d’air comprimé limité, et de l’eau et de l’huile dans les circuits d'air
M. Labarthe a sollicité BEKO TECHNOLOGIES car il devait faire face à une problématique récurrente en termes de maintenance des installations d’air comprimé : « le site s’est fortement développé, l’usine a beaucoup grossi et la centrale de séchage, un sécheur par adsorption régénéré à chaud, commençait à montrer certaines limites. Le séchage n’était plus optimum. Nous retrouvions régulièrement de l’eau et de l’huile dans les circuits d’air, ce qui entraînait une détérioration progressive du matériel, et donc des interventions de plus en plus régulières de l’équipe de maintenance (30 collaborateurs) ainsi que des problèmes face au respect de la réglementation relative à la sécurité alimentaire. Différentes améliorations ont été effectuées par mon équipe au fil du temps, mais il était devenu nécessaire de renouveler la centrale car la solution n’était plus viable. »
Le besoin est clairement identifié : élimination de l’eau et de l’huile contenues dans le réseau d’air comprimé et surveillance de la qualité de l’air comprimé, renouvellement de la centrale par une solution de traitement d’air comprimé plus performante et enfin, réduction des interventions de maintenance.
Plusieurs études ont été menées par M. Labarthe et son choix s’est finalement porté sur la solution préconisée par BEKO TECHNOLOGIES : « au-delà de la réputation de BEKO TECHNOLOGIES, l’approche technique et commerciale m’a séduit. BEKO a su aborder l‘ensemble des problématiques en lien avec le projet et ce, sur la base des exigences importantes de l‘installation du fait de son fonctionnement dans des conditions de températures très élevées, surtout en été. De plus, c’était le seul fabricant à proposer une solution globale, avec un sécheur comportant un process parfaitement adapté aux particularités et aux contraintes de notre production d‘air comprimé. »
Une solution technique complète, performante, fiable et économe
La solution est composée d’un ensemble de pré-refroidissement comportant un échangeur tubulaire de type air/eau à faisceaux démontables, un séparateur cyclonique équipé d’un purgeur automatique BEKOMAT®, et un dispositif de régulation de la boucle d’eau glacée. D’un ensemble de filtration CLEARPOINT® pour éliminer l’eau, les particules solides, les poussières et l’huile contenues dans l’air comprimé. D’un sécheur par adsorption à régénération par apport de chaleur EVERDRY® permettant d’obtenir un point de rosée très bas, et ce, sans consommation d’air comprimé.
De plusieurs purgeurs de condensats BEKOMAT® pour évacuer les condensats provenant de l’installation d’air comprimé. Et d’un analyseur de la présence d’huile résiduelle dans les réseaux d’air comprimé METPOINT® OCV compact.
Les compresseurs n’ont pas été changés mais la cuve de 500 litres en sortie a été remplacée par une cuve d’une capacité supérieure.
La réalisation d’une économie annuelle considérable et une satisfaction complète du client
Plus de 15 mois après la mise en service de l’installation par le SAV de BEKO TECHNOLOGIES, le bilan s’avère très positif. Le sécheur par adsorption EVERDRY® a permis d’obtenir un PRSP très bas et constant d’au moins -61 °C, même en cas de fortes chaleurs. Les prolongations de cycles obtenues par le sécheur ont répondu très favorablement à l‘aspect énergétique recherché, en permettant la réalisation d’économies conséquentes.
« Nous n’effectuons plus aujourd’hui de dépannage des installations lié à la présence d’eau et d’huile dans les circuits et, de ce fait, nous n’avons plus de temps d’arrêt de la production », se réjouit Thierry Labarthe. « En ce qui concerne les normes alimentaires encadrant notre activité, la nouvelle installation nous a également permis de progresser, puisque nous sommes passés de deux à un nettoyage mensuel des filtres stériles. À cela, il faut rajouter une baisse significative du temps d‘engagement des compresseurs. » En effet, alors que l’ancienne installation fonctionnait avec 4 compresseurs, le sécheur EVERDRY® a permis de supprimer un compresseur de 55kW et de n’utiliser plus que 3 compresseurs sur 5 au total. Ce changement engendre un gain de 472 MWh, soit une économie financière annuelle d’environ 38 000 €, équivalent à environ 210 tonnes de CO2. À ces gains d‘exploitation, il faut ajouter une diminution drastique des opérations de maintenance liées à l’air comprimé.
Les bénéfices tirés par Grands Chais de France de l’installation réalisée par BEKO TECHNOLOGIES sont d’autant plus intéressants que son potentiel n’est pas encore complètement exploité. « Aujourd’hui, le nouveau sécheur tourne à 50 % de ses capacités », confirme M. Labarthe. « Nous pouvons d’ores et déjà augmenter la puissance par le biais de l’ensemble des compresseurs, et si demain nous souhaitons en exploiter pleinement les capacités, il nous suffira d’ajouter des compresseurs ou de les remplacer par d’autres, plus performants. » . Et de conclure : « conseil, accompagnement, mise en place… tout a été parfait ! Pour d‘éventuels projets futurs, nous n‘hésiterons pas à faire de nouveau appel à l‘expertise de BEKO TECHNOLOGIES. »