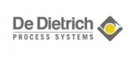
De Dietrich renforce ses activités dans la chimie du végétal
21/08/2017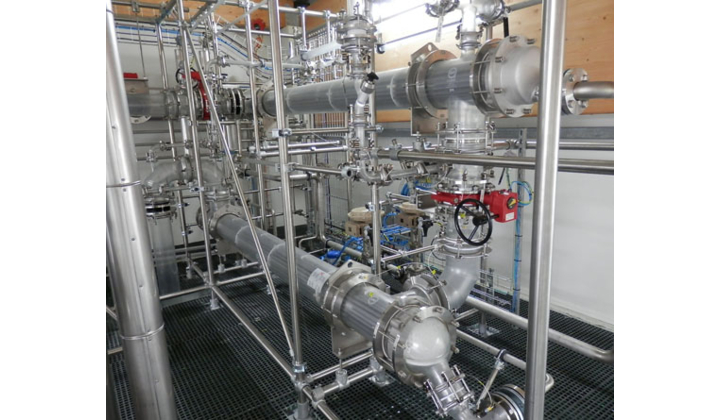
Bien que déjà présent auprès d’acteurs majeurs de ce secteur, la mise en place d’une organisation dédiée au sein du groupe traduit la volonté du Groupe d’accompagner ses clients toujours plus loin dans le développement de produits biosourcés performants et innovants.
Fort de 333 ans d’expertise technique, de ses compétences en ingénierie et de sa présence internationale, De Dietrich Process Systems propose ainsi aux industriels de l’Alimentaire, de la Santé, de la Cosmétique et des Bio Matériaux, un ensemble complet de solutions sur mesure et clé-en-main, pour l’extraction et la purification d’ingrédients et d’actifs à partir de biomasse. Ces solutions sont notamment mises en oeuvre dans la production de colorants naturels, d’exhausteurs de goûts, d’arômes, d’huiles essentielles raffinées, d’extraits botaniques ou encore de texturants.
Les technologies intégrées dans les procédés mis en oeuvre par DDPS couvrent en particulier l’extraction solide-liquide et liquide-liquide, l’évaporation-concentration sous vide, la distillation fractionnée, la filtration, le séchage, l’hydrodistillation et la distillation moléculaire. En phase amont des projets, les outils DDPS de simulation et d’essais facilitent la définition et l’optimisation des paramètres opératoires, tandis que les capacités internes de production et d’intégration de DDPS permettent d’envisager la réalisation des projets industriels qui en découlent, sans limitation de taille.
Dans une première étape, DDPS a ouvert un bureau commercial à Grasse (France) et s’appuiera sur ses unités d’ingénierie de Barcelone (Espagne), Zinswiller (France) et Mayence (Allemagne) pour l’Europe, de Charlotte (NC) pour les USA et Wuxi (Chine), Rabale (Inde) et Singapour pour l’Asie.
Une volonté ambitieuse illustrée avec succès par le récent partenariat avec la société SAS PIVERT à Compiègne (www.sas-pivert.com), pour laquelle DDPS a développé un outil pilote dédié à la valorisation de la biomasse oléagineuse. Le pilote est constitué d’une unité réactionnelle sous pression, d’une colonne de fractionnement sous vide continue, d’un ensemble de condensation-décantation-stockage, et des périphériques associés (skid de vide, skid thermique, pompes de transfert, structure support…). Le tout est complété par un skid de séchage sous vide (sécheur vertical agité) avec transfert automatique des solides pour les phases de chargement du sécheur.