Choisir une pompe à membranes: les critères de choix
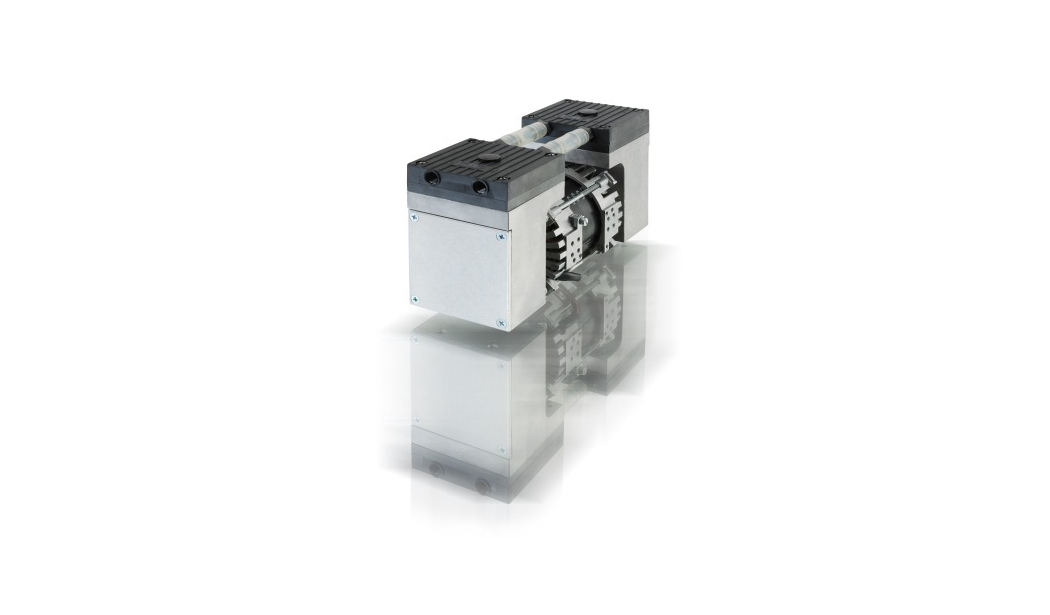
Pour choisir une pompe à membranes pour véhiculer des gaz ou des liquides, un certain nombre de critères de choix sont généralement bien identifiés lorsque le choix doit s'opérer. Il ne faut néanmoins pas oublier que outre des critères comme le débit souhaité, le niveau de vide ou de pression désiré, les pertes de charges, la compatibilité chimique des matériaux et la température, d'autres éléments doivent également entrer en ligne de compte pour effectuer ce choix.
En effet, 12 paramètres décisifs sont à intégrer pour choisir une pompe à membranes:
1-Etanchéité du système et niveau de fuites acceptable.
Il s'agit dans un premier temps déterminer le niveau de fuite acceptable pour votre application. Dans le cas d’une pompe à gaz, il s’agit des fuites de gaz qui s’échappent de l’intérieur de la pompe vers l’extérieur ou au contraire, de l’air extérieur qui pourrait s’introduire dans la pompe (avec risque de dilution de l’échantillon). Par conception, la majorité des pompes présentent une étanchéité de l’ordre de 6X10-3mbar.l/s (variation de pression en mbar donnée pour un volume de 1litre et un temps de 1sec). Des solutions existent cependant pour renforcer cette étanchéité avec notamment l’ajout d’une membrane de sécurité permettant ainsi un niveau de fuite de l’ordre de 6X10-6mbar.l/s. Cela s’avère intéressant, notamment dans le cas d’un transfert de gaz rares, toxiques ou radioactifs (fuites vers l’extérieur) ou pour préserver la nature d’un gaz à analyser (fuites vers l’intérieur).
2-La pompe n’est pas une vanne. Elle est passante !
Les clapets à l’intérieur de la pompe ne sont généralement pas conçus pour être absolument étanches lorsque la pompe est à l’arrêt. En effet, la pompe n’est pas un organe d’isolement. Si un isolement est nécessaire, des solutions simples existent comme l’ajout d’un clapet anti-retour, d’une vanne d’arrêt ou d’une valve de régulation de pression (déversoir à membrane).
3-Le risque de siphonage.
Dans le cas d’un transfert dans des conduites avec une vitesse de fluide plus importante, un effet venturi peut se produire et engendrer un phénomène d’aspiration. Cela signifie que, lorsque la pompe est à l’arrêt, l’aspiration produite par l’effet venturi peut dépasser la résistance des clapets de la pompe et forcer un passage du gaz ou liquide au travers de celle-ci. Avec l’intégration d’un déversoir à membrane entre la pompe et la conduite incriminée, l’effet venturi sera stoppé.
4-Le phénomène de pulsation.
La technologie de la pompe à membrane implique un mouvement alternatif d’ouverture et de fermeture des clapets qui permet la création du flux de gaz ou de liquides dans la tête de pompe. Un phénomène de pulsations plus ou moins important peut en résulter. Pour certaines applications qui l’exigent, on peut réduire ce phénomène de plusieurs manières : par l’ajout d’un amortisseur de pulsation, par l’insertion d’un volume mort dans le circuit (atténuateur), par le déplacement de la pompe dans le système ou par la modification des tuyaux (diamètre, longueur, dureté). On peut aussi agir sur la pompe directement en sélectionnant une vitesse de moteur adaptée ou pourquoi pas en privilégiant une pompe à deux têtes.
5-Le bruit, le niveau sonore.
La première étape pour atténuer le bruit d’une pompe à membrane est de déterminer son origine. Ce bruit peut être mécanique et/ou pneumatique. Le bruit pneumatique qui sort de la pompe peut être facilement et considérablement réduit par l’utilisation d’un filtre/silencieux à l’aspiration et/ou au refoulement. Pour le bruit mécanique, les solutions peuvent être l’ajout de plots anti-vibratiles, le choix d’un moteur plus silencieux, la réduction de la vitesse du moteur, l’ajout d’une coque d’insonorisation… Les solutions sont multiples !
6-La compatibilité électromagnétique CEM.
L’ensemble d’un système ou certains équipements peuvent être sensibles aux émissions électriques des moteurs à courant alternatif ou courant continu. Les normes CE actuelles permettent de lutter contre les émissions électriques (électromagnétiques) des pompes mais aussi de protéger celles-ci contre les perturbations/ émissions provenant d’autres équipements voisins.
7-La régulation de la vitesse du moteur.
Faire correspondre la vitesse du moteur de la pompe aux besoins réels de l’application permet de réduire les contraintes sur la pompe (stress) ou sur les autres composants du système et donc d’augmenter la durée de vie, de consommer moins d’énergie, de produire moins de chaleur, de générer moins de bruit et de vibrations. Les performances des pompes à membrane varient en fonction de la vitesse du moteur. Il est également possible de modifier mécaniquement la pompe afin de « caler » les performances sur votre besoin.
8-Démarrage en contre-pression ou sous vide.
La plupart des pompes ne sont pas conçues pour démarrer (ou redémarrer) en charge (pression ou vide). Une simple modification mécanique au niveau des clapets et/ou la sélection d’un moteur plus puissant peuvent être la solution pour répondre à cette exigence tout en assurant une longue durée de vie de la pompe. Ces solutions simples et économiques permettent également d’éviter des modifications complexes et coûteuses du système extérieur à la pompe.
9-Risque de condensation.
La compression d’un gaz humide lors du pompage entraine la formation de condensats à l’intérieur de la pompe voire une accumulation qui peut provoquer une défaillance de la pompe. La position de la pompe lors de son intégration peut suffire à éviter cette accumulation de condensats. En effet, il faut faciliter l’écoulement naturel par gravité des condensats vers le refoulement de la pompe et si possible, veillez à ce que la pompe soit en position haute par rapport au système.
10-Risque de cavitation.
Ce phénomène se produit lorsque la pression d’un liquide tombe au-dessous de sa pression de vapeur. Cela peut être le cas lors de l’aspiration. Le comportement du fluide change et les performances ainsi que la durée de vie de la pompe peuvent se réduire. Cette situation peut être évitée par l’utilisation d’un tuyau adapté (diamètre, dureté) ou alors par la modification de la course de la membrane ou la vitesse d’aspiration du fluide. Attention donc aux applications avec des solvants liquides et volatiles pour lesquels le risque de cavitation à l’aspiration est plus fréquent !
11-Risque de surpression.
Lorsqu'un risque de surpression existe, il convient parfois de prévoir une protection contre les dommages consécutifs à une surpression liée à une panne, une erreur ou un blocage éventuel (filtre colmaté par exemple) ? L’ajout d’un accessoire (soupape de sécurité, un limiteur de pression…) protégera donc la pompe, le moteur, les conduites, les vannes, les filtres… ainsi que les appareils sensibles qui pourraient également se trouver connectés au circuit (analyseur, débitmètre…).
12-L’altitude.
Le débit d’une pompe varie en fonction de son altitude d’implantation. Les performances sont fréquemment données pour un fonctionnement au niveau de la mer (altitude 0m). Par ailleurs, la valeur de la pression barométrique du jour a également une incidence sur les performances de la pompe (son vide limite par exemple).
Le choix d'une pompe à membrane fait donc appel à une multitudes de critères qui vont bien au delà du simple débit, du niveau de vide et de pression souhaité désiré. Les solutions offertes par les fabricants de pompes à membranes sont nombreuses afin de répondre aux mieux à ces critères. KNF ayant de son côté développé une offre de pompes à membrane qui répond à cette multitudes de critères.
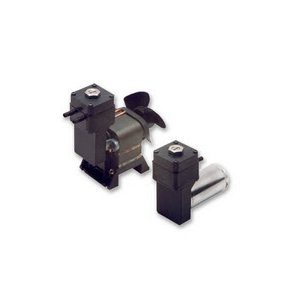
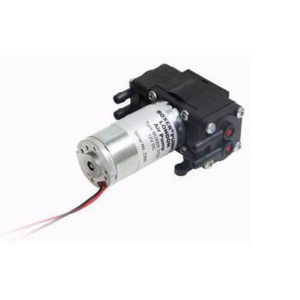
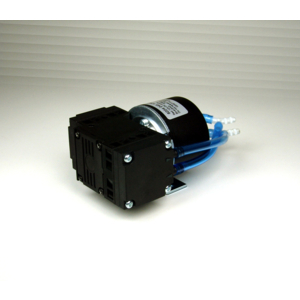
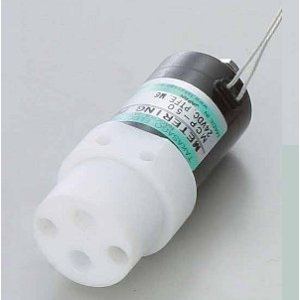
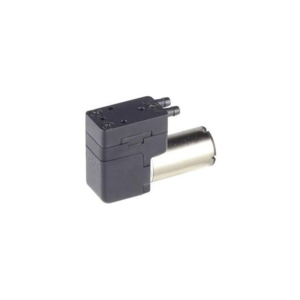
Mini pompes à membrane série 20K

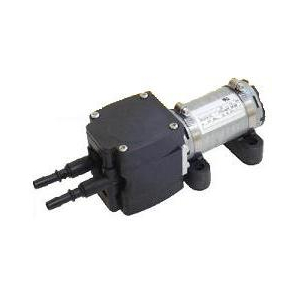