La transformation digitale change l'industrie
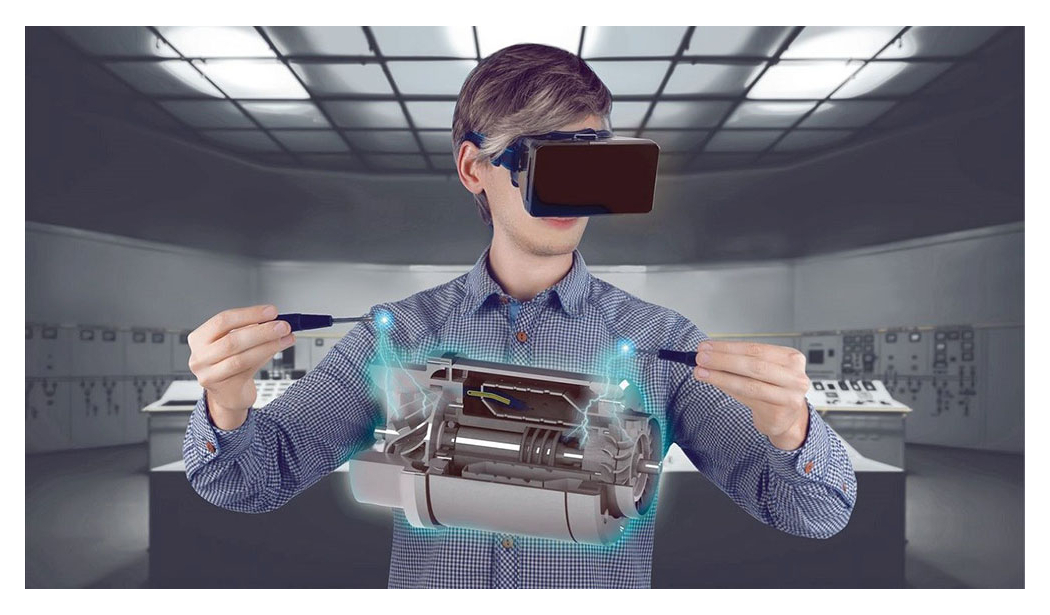
Le monde manufacturier mondial semble remonter le temps. Les grandes usines de production et les longues chaînes d'assemblage, où les marchandises ont été produites en masse par plusieurs et par milliers, pourraient bien appartenir au passé. Au lieu de cela, nous assistons à une demande croissante de produits hautement personnalisés en fonction des besoins de chaque client final. Cela ressemble beaucoup aux années précédant la première révolution industrielle, où chaque produit était minutieusement fabriqué à la main.
L’industrie mue
Pour éviter que les employés ne passent des heures à créer des produits sur mesure, l'industrie peut désormais produire rapidement des millions de biens, en lots de plus en plus petits, sans faire de compromis sur la qualité ou la productivité. Cette transformation est possible dans un écosystème numérique axé sur les données et alimenté par des dispositifs et des solutions connectées qui maximisent le potentiel des infrastructures existantes.
En termes simples, la transformation numérique des entreprises capitalise sur les avantages des outils numériques tels que les capteurs intelligents, le Cloud Computing et l'Internet pour ajouter de la valeur aux processus de fabrication existants. La numérisation d'un processus de production ouvre de nouvelles possibilités afin de recueillir des informations utiles qui peuvent être analysées pour mieux comprendre l'état de chaque pièce d'équipement. Les capteurs d'une machine suivent en permanence son état et peuvent alerter immédiatement les opérateurs en cas d'anomalie dans les paramètres de fonctionnement normaux. La digitalisation garantit aux opérateurs de passer de la réaction aux incidents dans l'atelier à la maintenance proactive de leur équipement pour éviter les temps d'arrêt imprévus. Cela oblige les fabricants à respecter des délais de plus en plus exigeants, même en produisant une plus grande variété de produits.
Construire un écosystème digital
Dans un monde où la complexité et la concurrence ne cessent de croître, la digitalisation peut donner un coup de fouet à la productivité des équipements industriels. L’installation (facile) d’un capteur sur des machines thermosensibles, comme un robot de soudage, peut aider un opérateur à suivre les variations de température pour s’assurer que la température optimale est maintenue pour la soudure la plus parfaite du robot. L'amélioration de la transparence des processus dans une usine augmente la productivité, mais aussi des économies de ressources importantes grâce à la réduction des arrêts imprévus, et peut augmenter le cycle de vie et diminuer la consommation d'énergie des équipements.
Bien sûr, la plus grande valeur de la transformation digitale des industries peut être obtenue lorsque chaque pièce d'équipement de la chaîne de valeur est connectée. Que ce soit directement sur le lieu de travail ou via l'Internet industriel des objets. Les actifs connectés numériquement qui comprennent les informations transmises dans l'atelier peuvent interagir de manière autonome, conférant aux industries une toute nouvelle dimension d'efficacité et d'autonomie.
La bonne stratégie digitale à choisir
Les statistiques concernant la transformation digitale sont très encourageantes. Un rapport de 2019 du cabinet d'études de marché IDC a estimé que l'investissement direct dans la transformation numérique approcherait le chiffre stupéfiant de 7,4 mille milliards de dollars d'ici 2023 Mais d'un autre côté, il n'est pas rare de voir les stratégies de transformation numérique ne pas atteindre leurs objectifs alors que les entreprises luttent pour trouver la bonne approche et des employés qui peuvent relever le défi d'une refonte complète de leurs modèles d'entreprise.
Depuis 60 ans, ABB est à la pointe du développement et du déploiement de la technologie pour la fabrication numérique. L'introduction du premier robot à commande numérique au monde en 1974 n'est qu'un exemple parmi d'autres. Aujourd'hui, ABB, en tant que leader technologique, est le moteur de la transformation digitale des industries. Et maîtrise tous les éléments de la quatrième révolution industrielle qui représente la prochaine vague d'innovations, notamment l'IoT, l'intelligence artificielle et la fabrication modulaire pour soutenir les grandes et les petites entreprises, telle que l'intelligence artificielle se trouvant au cœur d'une solution qu'ABB a co-créée avec Microsoft pour aider une pêcherie de saumon nordique à suivre à distance sa population de poissons, réduisant ainsi le besoin d'intervention humaine et rendant finalement la production de plus de 70 000 tonnes de saumon par an plus durable.
La transformation digitale en temps réel
L'une des pierres angulaires des transformations numériques et de l'usine du futur est la capacité d'agir en temps réel, qui permet aux entreprises de répondre rapidement aux problèmes avant qu'ils ne se transforment en difficultés. C'est pourquoi, ABB pense que les progrès qu'il a réalisé avec ses partenaires de télécommunications Ericsson et Swisscom dans le domaine des communications 5G sont si passionnants.
Lors du Forum économique mondial de Davos, en Suisse, le robot collaborateur YuMi d'ABB a gravé un message dans un bac à sable qui a été reproduit en même temps par un second robot YuMi situé à 1,5 km de là. Cette démonstration de communication à faible latence sur de longues distances rendue possible par la 5G peut contribuer à concrétiser les futurs concepts de fabrication plus souples et modulaires. Les réseaux 5G sur une zone déterminée peuvent connecter des milliers de véhicules guidés automatisés qui se déplacent dans l'usine et apportent les pièces essentielles aux centres de production dans un délai très court.
Tout comme la production de masse, les dessins sur papier et les schémas traditionnels en 2D trouveront moins d'utilisateurs à mesurer que le monde industriel deviendra plus numérique. Ils sont remplacés par des concepts tels que les jumeaux numériques, où une image virtuelle entièrement fonctionnelle d'un bien physique est créée pour aider les opérateurs à régler des détails tels que tester l'interaction d'une machine avec son environnement. Les jumeaux numériques garantissent aux entreprises de perdre du temps à perfectionner et de tester des prototypes ou des modifications de produits et de réduire les coûts de production.
Une transformation digitale en soi se produit dans les services industriels. Les solutions de surveillance avancées comme ABB Ability™ Connected Services, aident les entreprises à surveiller leurs actifs sur plusieurs sites avec un seul un seul système. Les services connectés appliqués aux robots d'ABB peuvent aider les entreprises à surveiller l'état de leur flotte, à diagnostiquer les anomalies, à les faire fonctionner à distance, à planifier les calendriers de maintenance en donnant la priorité aux robots les plus performants et à fournir une gestion de sauvegarde, dans le but de récupérer facilement et rapidement les données en cas de panne ou de modification indésirable des systèmes.
Grâce à la digitalisation, l'amélioration de l'efficacité et de la productivité, la réduction des incidents indésirables et la création d'un processus de fabrication plus fiable assurent la réduction de la consommation de ressources et la mise en place d’un processus de fabrication plus durable. La numérisation n'est pas une mode passagère ou un privilège des grandes entreprises, mais un élément fondamental de l'avenir des industries.